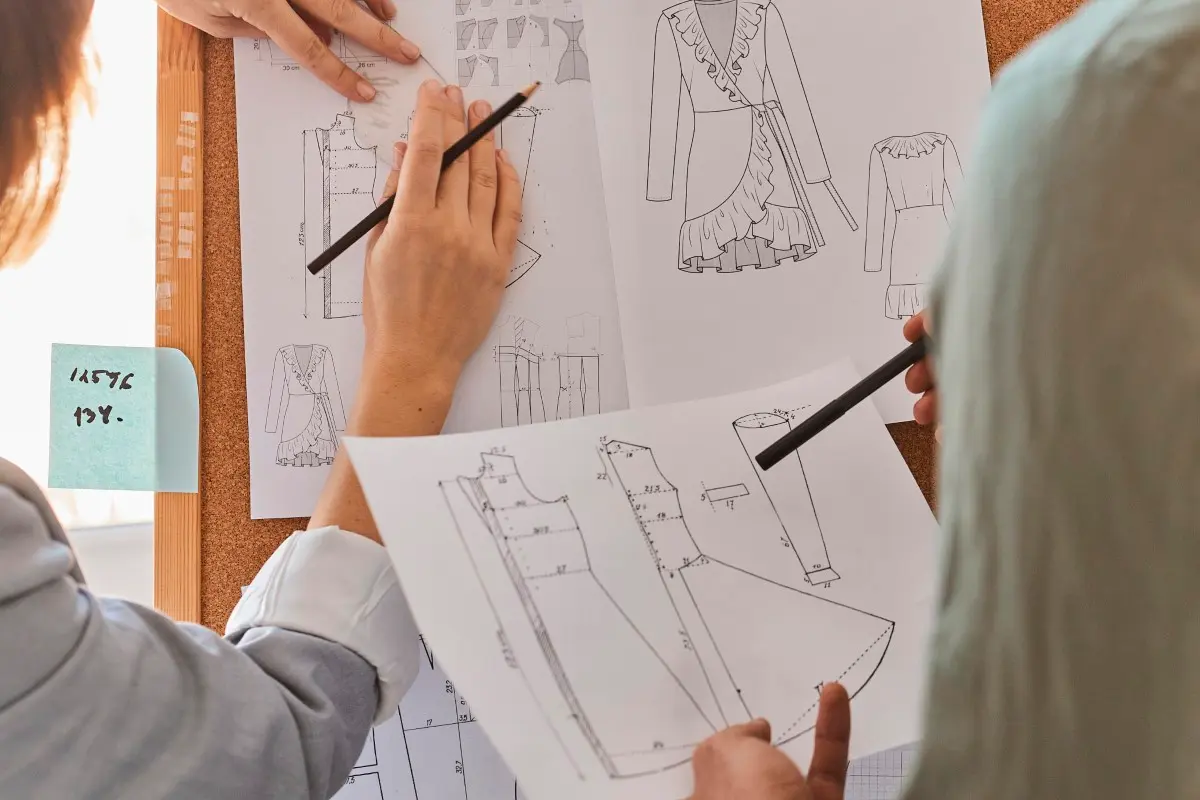
Apparel Prototypes
In the fashion industry, the journey from concept to creation involves many stages. One crucial step is creating apparel prototypes. These initial versions help designers visualize and perfect their ideas before full production begins. Prototypes play a key role in ensuring that a design meets expectations in terms of fit, style, and overall appearance, which is crucial for the success of any fashion business.
Let’s explore the importance of apparel prototype clothing in fashion and how it shapes the final product.
Introduction to Apparel Prototypes
Apparel prototypes are a crucial step in the fashion design process, allowing fashion designers to bring their ideas to life and test the quality, functionality, and aesthetics of their designs. In the fashion industry, prototyping is essential for fashion brands to ensure that their products meet the highest quality standards before proceeding to large-scale manufacturing. By creating a physical sample of their design, fashion designers can identify and fix design flaws, making adjustments to the pattern, fabric, and construction of the garment before producing the final product. This process is vital for fashion brands to stay competitive in the global market, where ethical manufacturing and attention to detail are highly valued.
What Is an Apparel Prototype?
An apparel prototype is a physical or digital sample of a garment. It serves as a model that represents the final design. The purpose of a prototype is to test how a garment looks, fits, and functions. Prototyping helps designers and manufacturers detect any potential issues early in the production process.
Prototype clothing can take many forms, depending on the type of garment being created. From simple T-shirts to complex evening gowns, each design requires its own approach.
Clothing Design Considerations
When creating a clothing design, fashion designers must consider various factors, including the target audience, body types, styling issues, and technical specifications. A good fashion designer must have a deep understanding of the manufacturing process and be able to communicate their ideas effectively to pattern makers, manufacturers, and other stakeholders. Technical sketches, tech packs, and prototypes are essential tools in the design process, allowing designers to refine their ideas and ensure that their vision is realized in the final product. Moreover, fashion designers must be aware of intellectual property protection and take steps to safeguard their designs from infringement. By considering these factors and working with experienced manufacturers like Billoomi Fashion, fashion designers can create high-quality, functional, and stylish garments that meet the needs of their target market.
Why Are Apparel Prototypes Important?
Prototypes are vital for several reasons. First, they allow designers to see how a garment looks in real life. A design that seems perfect on paper might not translate well in physical form. Apparel prototyping reveals how fabrics behave, how the garment fits, and whether any adjustments need to be made.
Prototyping services offer comprehensive support to fashion designers, ensuring that every aspect of the garment is meticulously tested and refined.
Second, sample apparel lets brands and designers test new ideas without committing to full production. It’s much more cost-effective to create a few prototypes than to produce an entire clothing line only to find that something is off.
Finally, fashion prototyping gives both designers and manufacturers the chance to collaborate and improve the design. Sometimes, a design looks great but is too expensive or difficult to produce. By working with prototypes, they can make changes that improve both the quality and the cost-effectiveness of the final product.
The Prototyping Process: From Idea to Sample Clothing
The prototyping process can be broken down into several steps:
- Conceptualization. Everything starts with a design concept. Designers sketch ideas and choose fabrics, colors, and trims. At this stage, they also consider the garment’s functionality and target audience.
- Pattern Making. Once the design is finalized, the first step is pattern making. A pattern serves as the blueprint for the garment. Skilled pattern makers create detailed instructions that guide the construction of the sample apparel.
- Creating the First Sample. The first version of the clothing sample is called a muslin. It’s typically made from inexpensive fabric to test the fit and structure. The goal is to see how the garment looks when worn and make any necessary adjustments.
- Fitting and Adjustments. Once the prototype clothing is complete, it undergoes a fitting session. This allows the designer to see how the garment fits on a model. Any issues with size, shape, or drape can be corrected at this stage.
- Final Prototype. After adjustments are made, a final apparel prototype is created. This version uses the actual fabric and materials intended for the final garment. The final prototype is a nearly identical version of the product that will eventually be sold to consumers.
- Approval and Production. The final step involves approval from the designer, brand, and manufacturer. Once the final prototype is approved, the garment moves into full production.
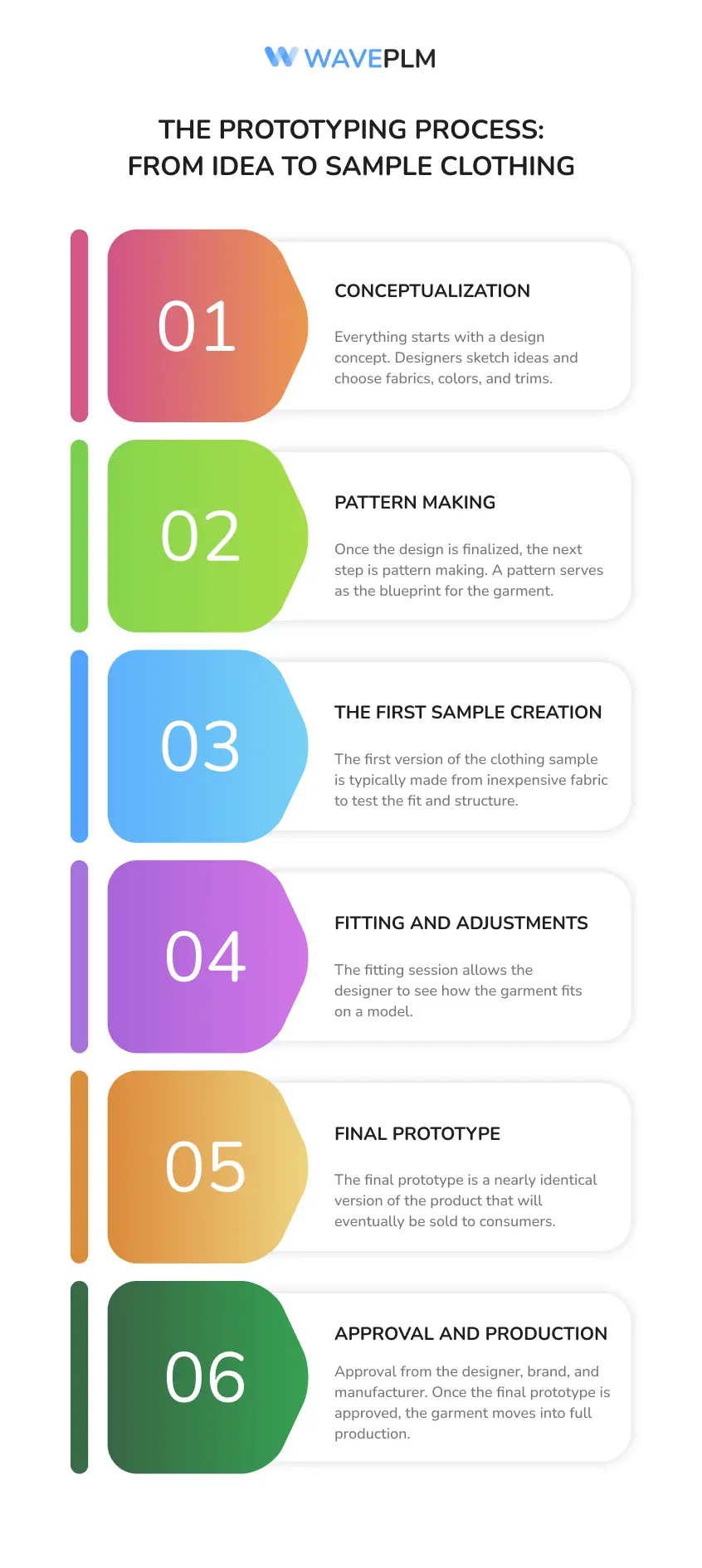
Apparel Prototyping Process
Garment Manufacturing Partnerships
Building strong partnerships with garment manufacturers is critical for fashion brands to succeed in the global market. A reliable manufacturer can provide high-quality materials, expert construction, and efficient production timelines, ensuring that the final product meets the brand’s quality standards. When selecting a manufacturing partner, fashion brands should consider factors such as ethical manufacturing practices, attention to detail, and ability to produce high-quality prototypes. By working with a trusted manufacturer, fashion brands can ensure that their products are produced with the best quality materials and construction methods, resulting in a final product that exceeds customer expectations. Additionally, a good manufacturing partner can provide valuable expertise and resources, helping fashion brands to navigate the complexities of the fashion industry and stay ahead of the competition.
Different Garment Types and Their Prototypes
Prototypes are used for all kinds of garment types, each with its own unique challenges.
- Tops and Blouses. These garments require careful attention to fit and construction. Prototypes help ensure that the neckline, sleeves, and torso fit comfortably and look stylish.
- Pants and Skirts. The fit of pants and skirts is particularly important. Prototype clothing allows designers to test how different fabrics affect the fit around the waist, hips, and legs.
- Outerwear. Coats and jackets often involve multiple layers and more complicated construction. Creating a sample clothing version allows for detailed testing of these garments’ insulation, fit, and durability.
- Dresses and Gowns. Dresses and evening gowns often feature intricate details and unique silhouettes. Prototypes help designers visualize how these garments move and drape on the body.
Developing prototypes for these garment types involves careful attention to detail and multiple iterations to ensure the final product meets design specifications.
Tips for Effective Prototyping
Effective prototyping is essential for fashion designers to test and refine their designs, identify design flaws, and ensure that their products meet the highest quality standards. Here are some tips for effective prototyping: first, create a detailed tech pack and technical sketches to communicate your design ideas clearly. Second, work with an experienced pattern maker to create a high-quality prototype that accurately represents your design. Third, test your prototype on different body types and gather feedback from potential customers to identify styling issues and areas for improvement. Fourth, make adjustments to your design based on the feedback and testing results, and finally, produce a physical sample of your design to test its functionality and quality. By following these tips and working with a trusted manufacturer, fashion designers can create high-quality prototypes that accurately represent their design vision and meet the needs of their target market.
Common Mistakes to Avoid
When creating apparel prototypes, there are several common mistakes to avoid. First, failing to create a detailed tech pack and technical sketches can lead to miscommunication with manufacturers and pattern makers, resulting in a prototype that does not accurately represent the design. Second, not testing the prototype on different body types can lead to styling issues and poor fit, resulting in a final product that does not meet customer expectations. Third, neglecting to consider the manufacturing process and materials can result in a prototype that is not feasible for large-scale production, leading to delays and increased costs. Fourth, failing to protect intellectual property can result in design infringement, leading to financial losses and damage to the brand’s reputation. By being aware of these common mistakes and taking steps to avoid them, fashion designers can ensure that their prototypes are effective, efficient, and accurate, resulting in a final product that meets the highest quality standards and exceeds customer expectations.
The Impact of Technology on Fashion Prototyping
In recent years, technology has transformed fashion prototyping. Digital tools now allow designers to create 3D prototypes that simulate real-life fabrics and movements. These tools speed up the process, reduce waste, and allow for quicker adjustments. These tools help transform design concepts into reality by providing accurate simulations of fabrics and movements.
Product Lifecycle Management (PLM) software further enhances this process by streamlining communication and data sharing across teams. With PLM, designers, manufacturers, and suppliers can access real-time updates on prototypes, ensuring a more efficient workflow from concept to final production.
3D prototyping and PLM together help brands reduce the number of physical samples, cut production costs, and bring products to market faster. This not only improves efficiency but also makes the process more sustainable.
Key Benefits of Apparel Prototyping
- Cost Efficiency
Prototyping reduces costs by identifying problems early. Brands save money by avoiding the mass production of flawed garments.
- Improved Fit and Quality
Testing with a clothing sample ensures the final product fits well and meets quality standards. Each prototype is rigorously tested to ensure it meets the highest quality standards before moving to full production. This improves customer satisfaction and brand reputation.
- Speed to Market
Prototyping streamlines the design and production process. This allows fashion brands to get their products to market faster, a crucial factor in the competitive fashion industry.
- Collaboration
Prototyping encourages collaboration between designers, manufacturers, and suppliers. Together, they work to improve the final product, ensuring it meets design and production standards.
Conclusion: The Future of Fashion Prototyping
As technology continues to advance, fashion prototyping is evolving rapidly. Digital tools and 3D modeling make the prototyping process faster and more efficient, reducing the need for multiple physical samples. PLM software plays a crucial role in this transformation by streamlining communication and data sharing across teams, ensuring that every step from design to production is seamless.
Despite these innovations, physical prototypes will remain essential for testing fit, fabric, and overall garment quality. By integrating apparel prototypes with cutting-edge technologies like PLM, fashion brands can bring their ideas to life with greater accuracy, efficiency, and sustainability.
Prototyping bridges the gap between creativity and production, ensuring that every garment meets high standards before reaching consumers. As fashion continues to innovate, prototyping will remain a critical step in turning visionary designs into high-quality, ready-to-wear garments. The ongoing development of new technologies will continue to enhance the efficiency and accuracy of the prototyping process.