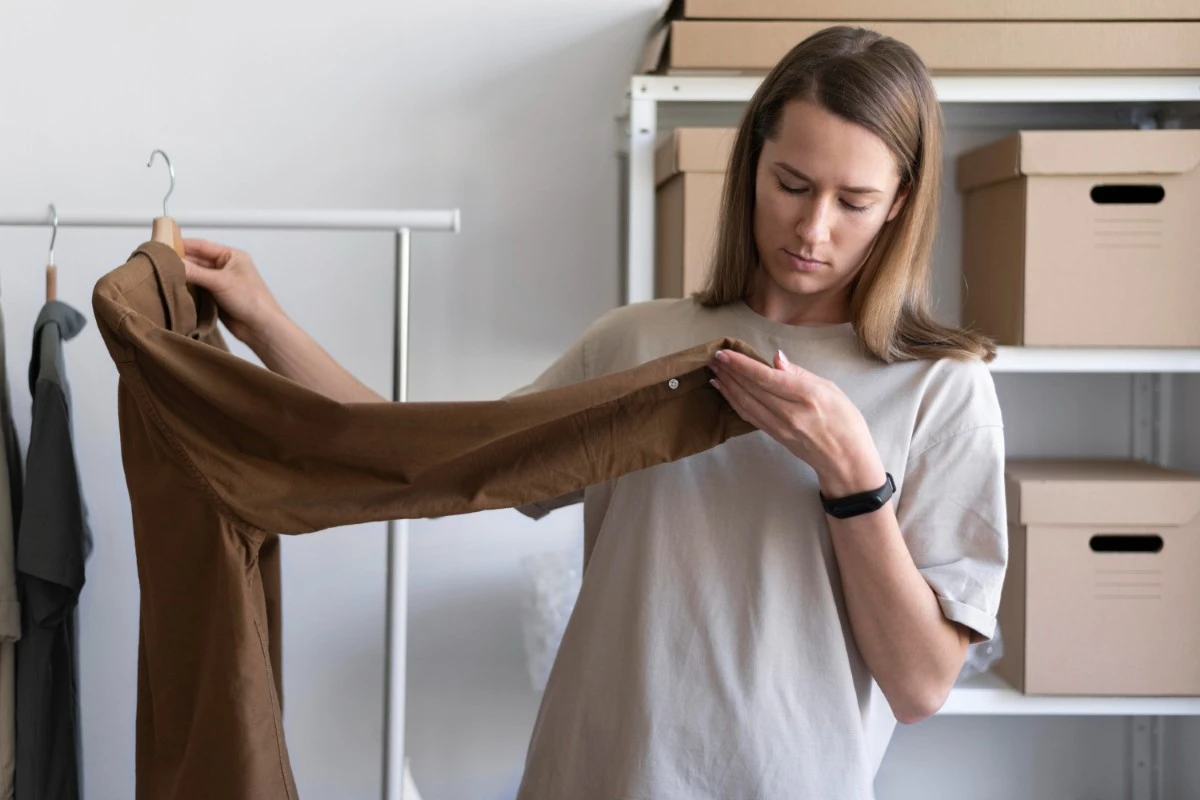
In the fashion industry, maintaining high quality is more than avoiding defective clothes. It’s about brand reputation, customer trust, and cost savings. A single poor-quality item can impact thousands of sales and trigger corrective actions across the supply chain.
Brands that invest in better quality assurance not only ensure customer satisfaction but also avoid long-term losses. Damaged reputation, costly product recalls, and excess waste can easily be prevented through a more streamlined, data-driven quality control process. This applies across every fashion sector, from high-end luxury to mass-market brands.
Every season introduces new fabrics, trims, technologies, and fits. Without strong quality assurance, even the most innovative product lines can fail. That’s why tracking, standardization, and structured communication are vital to maintain a competitive edge. As materials evolve and production scales, the ability to maintain quality across diverse product lines becomes a defining factor of brand success.
To stay competitive, fashion brands need a reliable way to manage raw materials, track changes, and prevent mistakes before they become costly. Therefore, embracing the right tools becomes essential. Quality assurance thrives in environments where clear data, real-time communication, and proactive systems are in place.
This is where BOM software and PLM tools come into play. These solutions offer detailed insights, traceability, and collaboration features. As a result, they empower teams to anticipate problems rather than simply reacting to them. In the long run, this makes quality assurance a built-in part of the workflow instead of a separate process. The integration of these tools into daily operations streamlines quality protocols, ensures better vendor alignment, and builds a continuous feedback loop that improves with every season.
Quality assurance extends beyond technical inspections. It reflects your brand’s promise. It encompasses garment durability, material authenticity, sizing consistency, and even the ethical sourcing of components. Customers notice when details are missing, when seams unravel, or when colors bleed. In a crowded marketplace, a proactive approach to quality assurance can be the deciding factor between loyalty and loss.
What Is a BOM in Fashion?
BOM stands for Bill of Material—a complete list of raw materials, components, and processes needed to create a finished product. This document acts as the single source of truth during the production cycle, helping teams keep every aspect aligned.
It’s not just a checklist—it’s a blueprint that guides design, development, and manufacturing. Every fabric, trim, label, stitch type, and even packaging detail should be documented in the BOM.
BOM Element | Example |
---|---|
Fabric | 100% organic cotton |
Trims | Buttons, zippers, labels |
Packaging | Eco-friendly polybags |
Labor & Overhead | Cutting, sewing, QC steps |
Technical Instructions | Stitch type, wash method |
A bill of material (BOM) is the core of any production process. It guides team members, factories, and vendors on what to use and how to produce the item. Meanwhile, a small error in the BOM can lead to production setbacks, increased costs, or quality failure. It also impacts sustainability goals and production timelines.
In many companies, the BOM also acts as the foundation for sourcing decisions, vendor communication, and compliance documentation. Consequently, its importance cannot be overstated. Well-organized BOMs help create consistency and repeatability across styles and seasons—two key pillars of effective quality assurance.
A structured BOM system supports a brand’s ability to scale. With each product referencing the correct materials, measurements, and specifications, teams avoid reinventing the wheel. They build on a centralized knowledge base that supports innovation without compromising control. Furthermore, BOMs can serve as the anchor point for audits, vendor negotiations, and performance evaluations.
The Problem: Manual BOMs Are Time-Consuming
Many brands still rely on spreadsheets or disconnected tools to manage their BOMs. That makes it:
- Time consuming to update
- Prone to human errors
- Difficult for quality control managers to follow
- Harder to manage product costing or track production planning
- Risky when different teams operate with different document versions
The reality is that as your collections grow and become more complex, the risk of errors and miscommunication also increases. Moreover, with fast fashion cycles and market-driven pressure, delays can significantly affect profitability.
Even minor mistakes—like forgetting to update a zipper color or using the wrong fabric code—can cost thousands. In fact, manual processes slow everyone down, creating bottlenecks at each step and jeopardizing quality assurance efforts across departments. The lack of integration means key information might not reach the right person at the right time.
Teams often scramble to verify if materials are approved, whether new specs have been uploaded, or if vendors are referencing outdated files. This reactive mode wastes time, causes tension across departments, and makes scaling difficult.
The Solution: PLM Tools with BOM Software
Fashion PLM stands for Product Lifecycle Management—a system that connects all product data, from concept to finished product. It creates a centralized platform where every stakeholder can work with the same up-to-date information.
By combining BOM software with PLM tools, fashion brands unlock a powerful framework for:
- Managing products across teams
- Making informed decisions
- Improving inventory management
- Reducing waste in the real world
- Gaining visibility into manufacturing processes
- Ensuring traceability and compliance with standards
- Strengthening communication with vendors and sourcing teams
- Embedding quality assurance directly into the product creation lifecycle
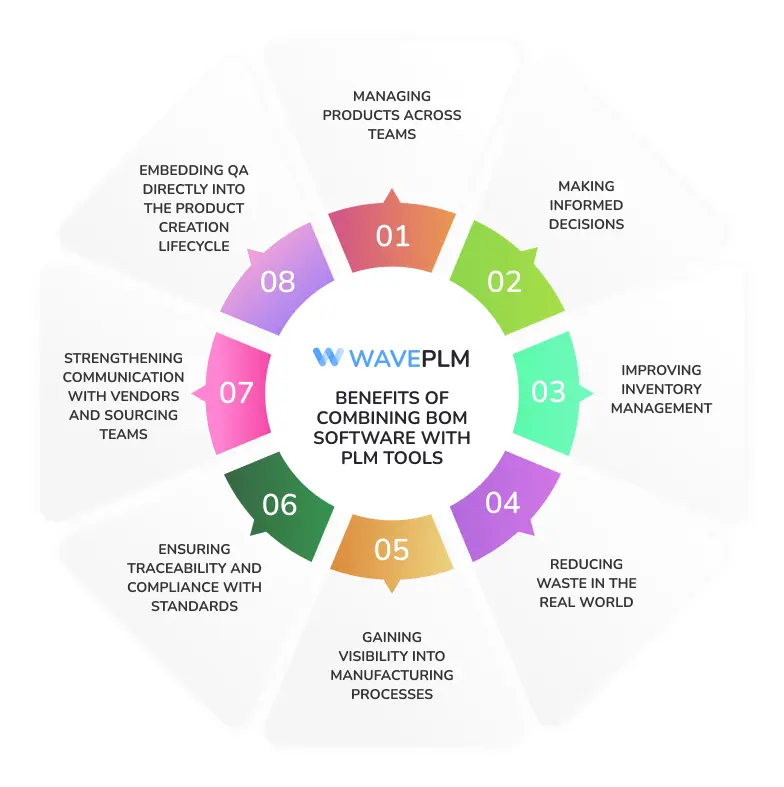
Wave PLM offers a fully integrated BOM and Quality Control (QC) App that works on phones and tablets—perfect for managers on the go. Not only does it streamline reporting, but it also enables mobile-first quality assurance that keeps pace with production on the ground.
This real-time access helps brands stay ahead of errors and provides a historical record of quality trends over time. Additionally, centralized data simplifies audits, performance reviews, and certification tracking. From the design room to the factory floor, Wave PLM enables seamless tracking of quality metrics and gives decision-makers the data they need to act with confidence.
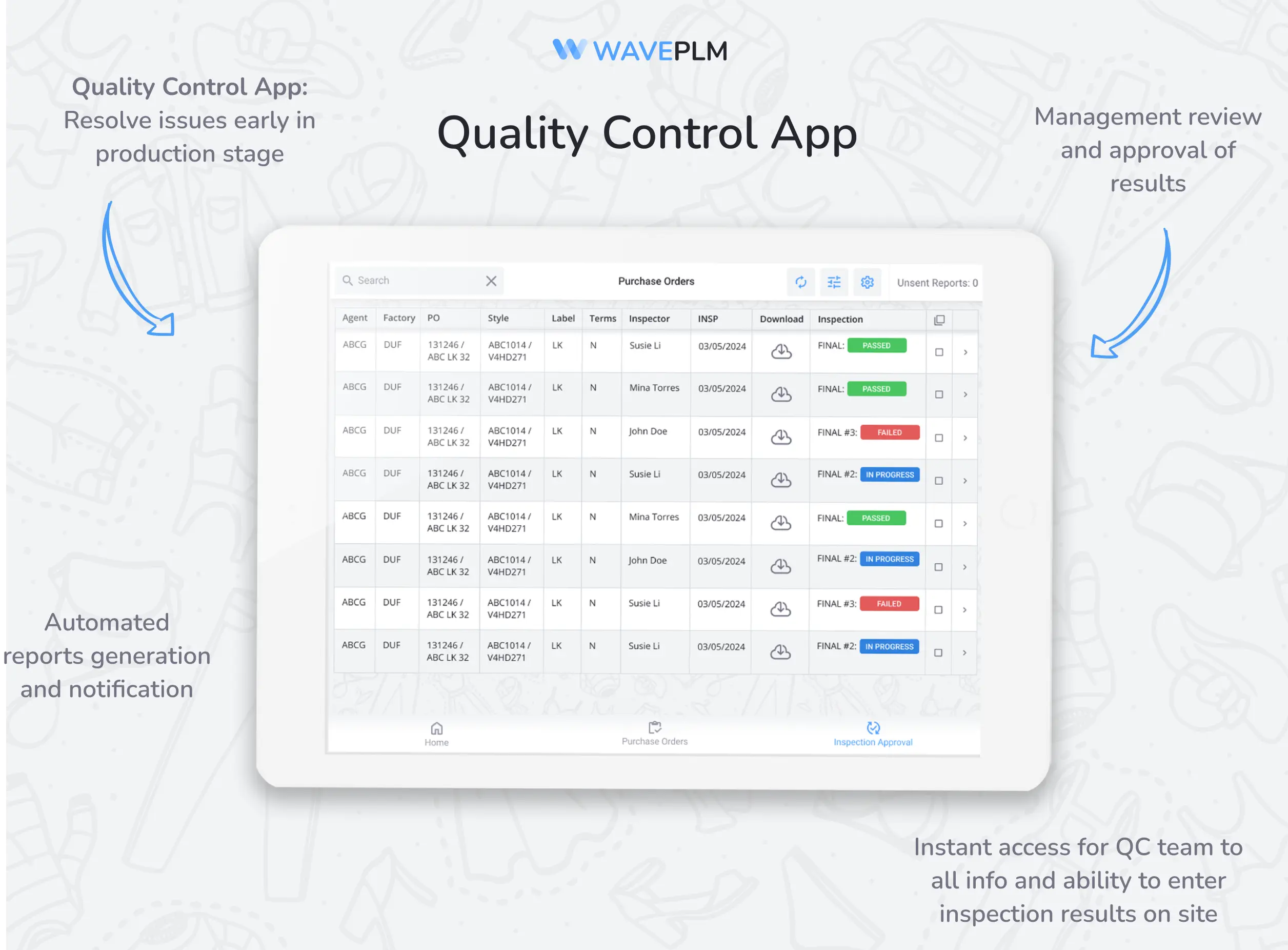
How BOM Software Supports Quality Assurance
Here’s how BOM software drives quality assurance in the fashion production process:
Quality Assurance Area | How BOM Software Helps |
Raw Material Standards | Link materials to specs for better sourcing |
Component Accuracy | Avoid mismatched trims or missing details |
Consistency | Use templates to replicate best practices |
Real-Time Updates | Sync changes with all team members |
Traceability | Track issues back to suppliers or materials |
Performance Checks | Monitor how different materials perform in testing |
Supplier Evaluation | Link BOMs with supplier scorecards |
Automated Alerts | Flag issues when data is missing or out-of-date |
Historical Data | Review previous issues to prevent future problems |
Factory Floor Insights | Combine BOM data with QC app reports for insights |
In practice, digitizing BOMs allows quality managers to identify weak points early and take corrective action before it’s too late. Moreover, combining these with mobile QC tools provides both macro and micro views of what needs to improve—where, when, and how.
Because quality assurance relies on speed and accuracy, integrated platforms like PLM help brands act immediately on insights, reduce rework, and protect the bottom line. The long-term value is undeniable—repeatable quality standards, improved compliance, and enhanced team efficiency.
Cost Control Through Better BOM Management
Beyond quality assurance, a well-managed bill of material helps brands gain control over product costing and budgeting.
Example:
Component | Cost per Unit | Supplier |
Denim fabric | $4.50 | Supplier A |
Metal zipper | $0.80 | Supplier B |
Thread | $0.20 | Supplier C |
Labor | $3.00 | Factory D |
Packaging | $0.50 | Internal |
With this view, fashion teams can:
- Spot areas for cost savings
- Forecast budgets more accurately
- Reduce waste from over-ordering
- Compare similar products for efficiency
- Simulate cost scenarios when raw material prices change
- Track how product design decisions impact overall cost
- Understand margin performance by style, category, or season
- Align quality assurance targets with profitability goals
Clear visibility into product cost also enhances the decision-making behind sourcing and assortment planning. Ultimately, better BOM management complements quality assurance by helping brands balance cost, speed, and consistency.
Final Thoughts
Managing quality and costs shouldn’t be a headache. With the right BOM software and PLM tools, fashion brands can:
- Make informed decisions at every stage of product development
- Track the entire production process with transparency and speed
- Cut unnecessary steps and reduce errors that slow teams down
- Deliver consistent quality across collections and seasons
- Increase profit margins by avoiding waste and cost overruns
- Stay competitive in a fast-changing fashion market
- Embed quality assurance in everyday processes
Quality assurance isn’t optional—it’s the foundation for customer trust, brand growth, and operational excellence.
📩 Ready to improve quality control and product margins?
Let’s talk about how Wave PLM can help.
Leave a Reply