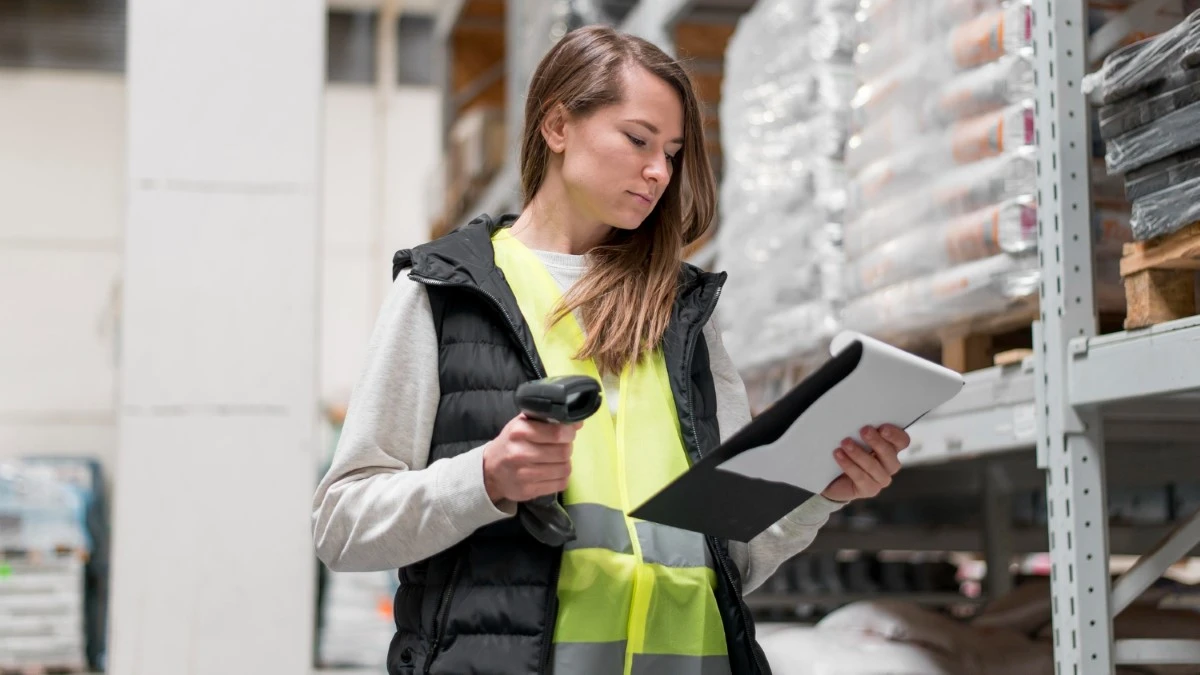
Efficient product returns play a critical role in modern manufacturing and shipping. Return Merchandise Authorization (RMA) simplifies this process, ensuring a smoother experience for both businesses and customers. In this article, we’ll make a definition of RMA (rma acronym), explain its importance, and explore how it streamlines returns while improving customer satisfaction.
What Does RMA Stand For?
RMA stands for Return Merchandise Authorization or Return Material Authorization. It refers to a formalized process that authorizes customers to return items. This system ensures that returned products are tracked, inspected, and processed efficiently. Whether you’re managing defective products or handling unwanted purchases, an RMA system is essential.
RMA Process Meaning: Why Is It Important?
Understanding the RMA definition is crucial in industries like manufacturing and shipping. Here’s why it matters:
- Streamlines Returns: RMA simplifies how businesses process return requests. Customers receive clear instructions, while businesses ensure efficient tracking of returned items.
- Improves Customer Satisfaction: A transparent and efficient RMA process makes customers feel valued. When they can return defective products or unwanted items without hassle, it boosts their trust in the brand.
- Enhances Quality Control: Managing product returns through an RMA system helps businesses identify recurring issues. This feedback loop improves products over time.
- Reduces Costs: Handling returns without an RMA system can lead to errors and inefficiencies. By defining a clear RMA process, businesses save time and money while reducing the risk of lost or mismanaged returns.
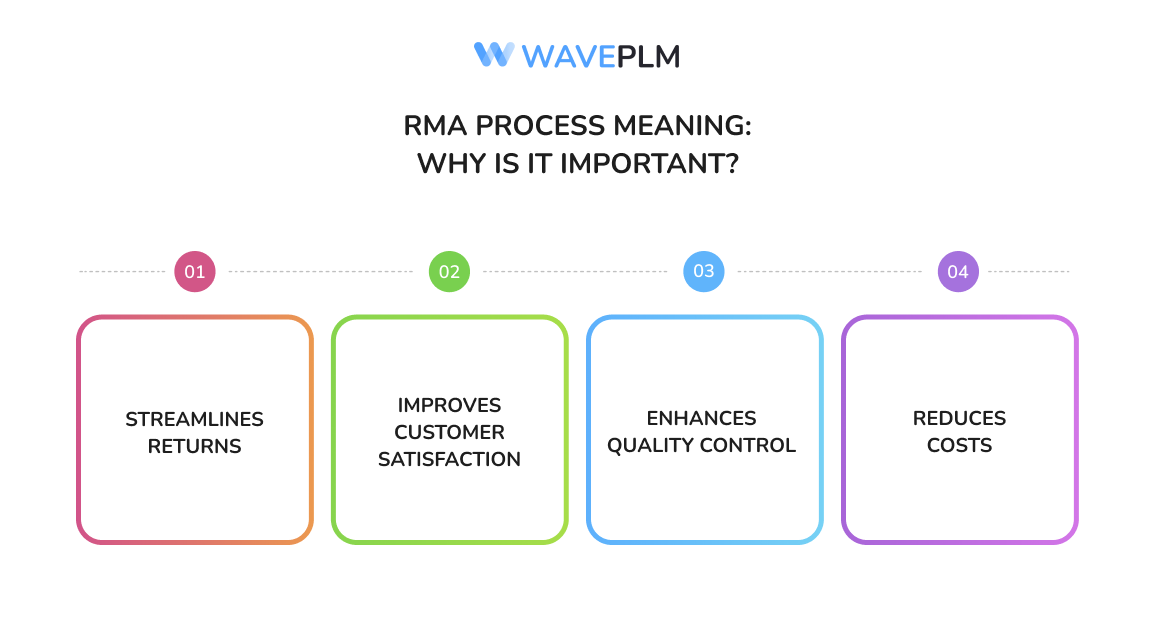
How Does an RMA Process Work?
The RMA process involves several key steps to ensure smooth returns. Let’s break it down:
1. Customer Initiates a Return
Customers request a return by contacting the seller or submitting an online RMA form. This step collects essential details like the product issue, order number, and customer contact information.
2. RMA Number Assigned
Once the return request is approved, the business assigns an RMA number (it’s a basic rma number definition). This unique identifier ensures the return is tracked through every stage.
3. Return Instructions Provided
The customer receives detailed instructions, including packaging guidelines and the shipping address. Clear communication reduces errors during this step.
4. Return Shipment
The customer returns the product using the provided instructions. In some cases, the business provides a prepaid shipping label to simplify the process.
5. Inspection and Processing
Once the product arrives, the business inspects it to verify the issue. Depending on the outcome, the company may issue a replacement, repair the item, or offer a refund.
6. Resolution
The final step resolves the issue to the customer’s satisfaction. This resolution could involve shipping a replacement, processing a refund, or repairing the product.
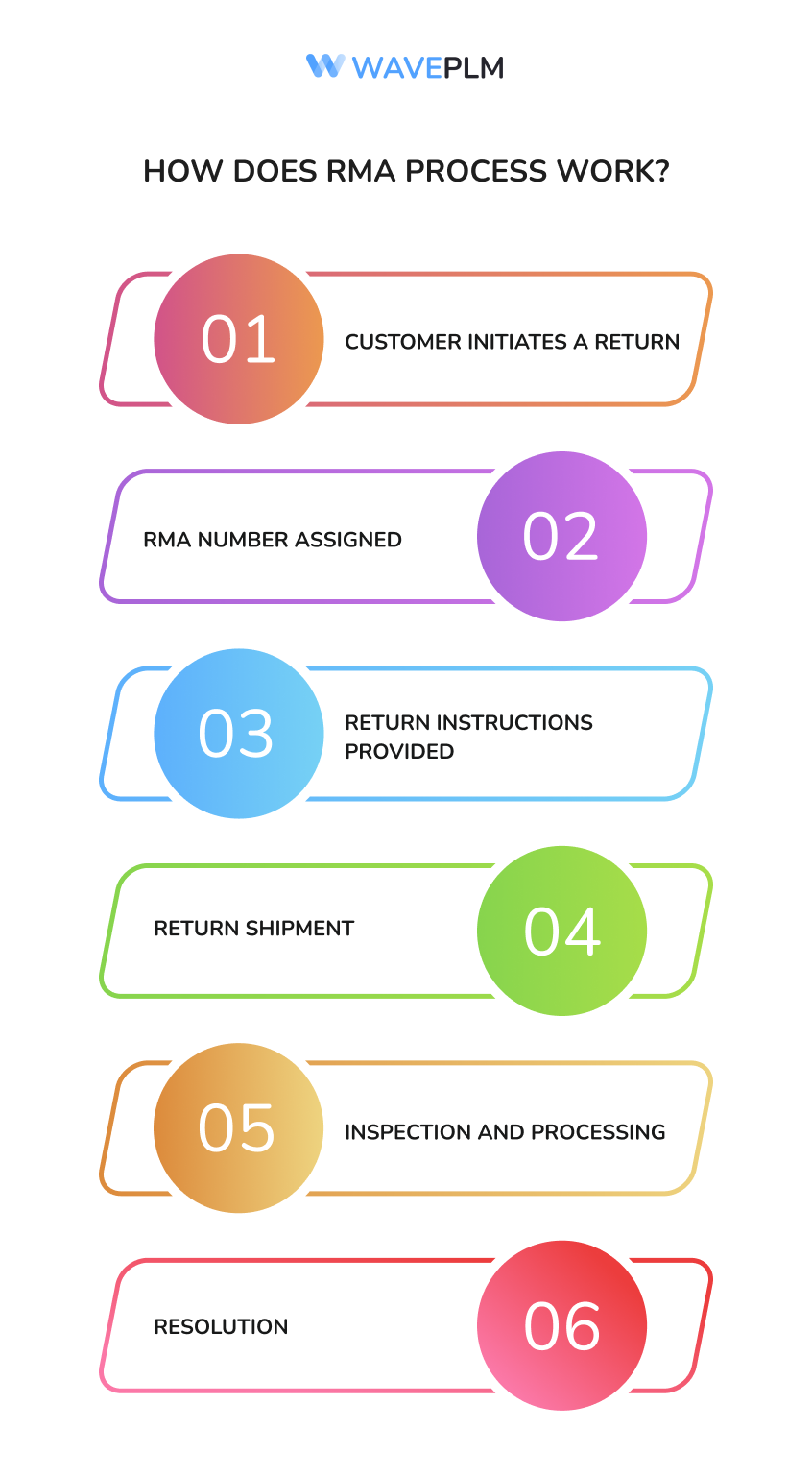
RMA in Manufacturing and Shipping
In manufacturing, RMA plays a crucial role in managing defective products. When a product fails quality control or experiences issues after shipping, the RMA process ensures it is returned efficiently. This system is vital for maintaining high production standards and customer trust.
In shipping, RMA helps resolve issues like damaged goods or incorrect orders. Reverse logistics, which involves moving products back through the supply chain, relies heavily on an effective RMA system. By defining the RMA process, companies streamline the return process and reduce logistical complexities.
Benefits of an RMA System
A robust RMA system or RMA software brings numerous advantages to businesses:
- Real-Time Tracking: Businesses can monitor return requests, ensuring no product is lost in the process.
- Efficiency in Processing Returns: Automated systems reduce manual work, speeding up the resolution of return requests.
- Improved Quality Control: By analyzing return trends, businesses can identify product defects and address them at the source.
- Cost Savings: Streamlined processes save money on shipping, labor, and inventory management.
- Customer Loyalty: Efficiently handling returns builds trust, increasing the likelihood of repeat business.
Integrating RMA with PLM Software
Integrating RMA with Product Lifecycle Management (PLM) software enhances the returns process significantly. PLM systems like Wave PLM provide a centralized platform to manage product data and ensure better coordination across teams. Here’s how integration benefits the RMA process:
- Seamless Data Exchange: Integration allows RMA data, such as return reasons and inspection results, to feed directly into the PLM system. This helps identify patterns in defects or quality issues.
- Faster Product Improvements: PLM tools uses RMA insights to adjust product designs or manufacturing processes, reducing future returns.
- Enhanced Collaboration: Teams across product design, manufacturing, and quality assurance can access real-time data, ensuring they address return-related issues promptly.
- Improved Compliance: For industries with strict regulations, integrating RMA and PLM tolls ensures all product returns and corrections meet compliance standards.
- Streamlined Workflows: Businesses eliminate redundancies by synchronizing return processes with product lifecycle stages. This saves time and reduces errors.
For companies already using PLM software, adding RMA integration is a logical step. It ensures end-to-end visibility of a product’s journey, from development to post-sale returns.
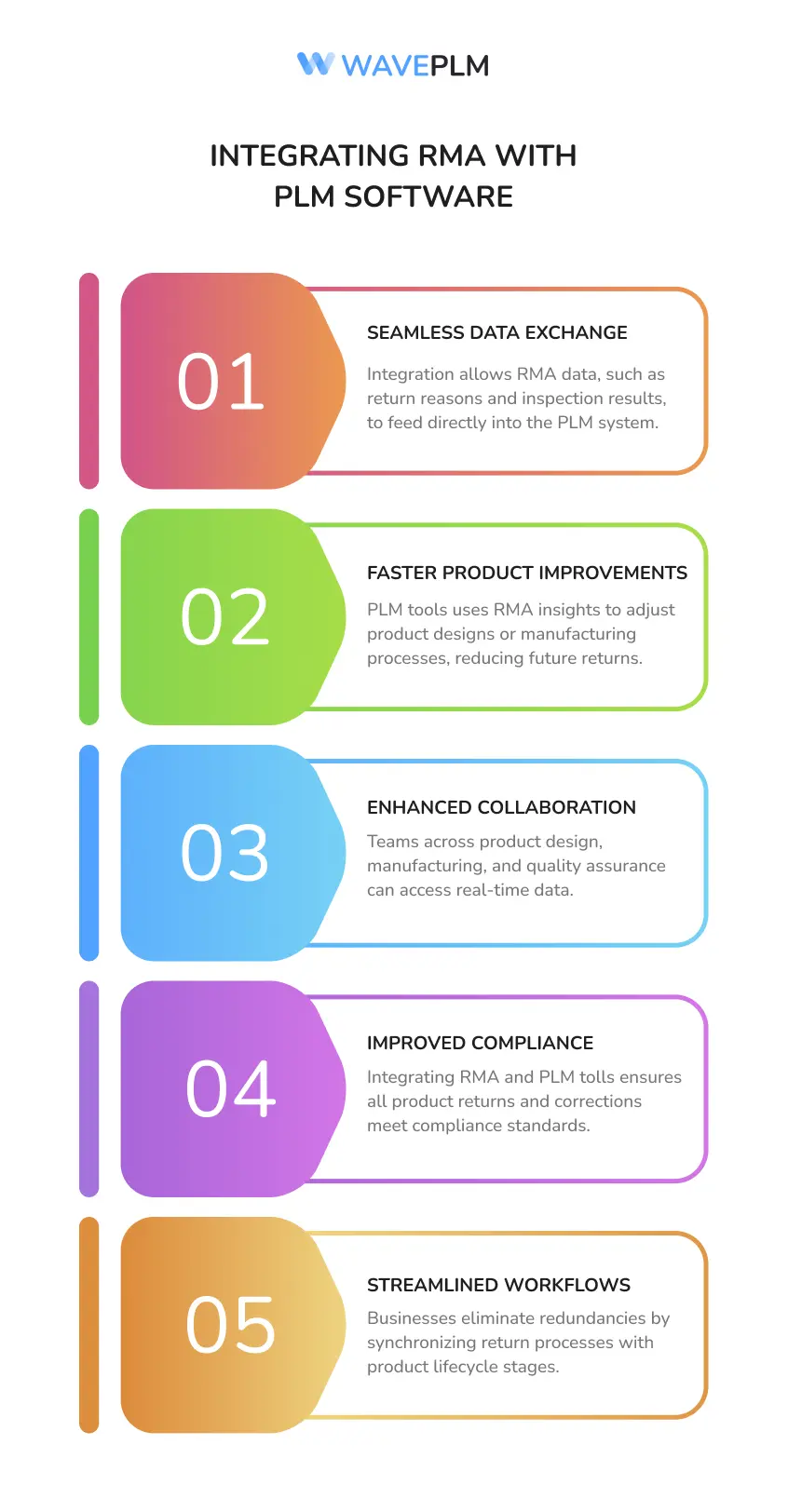
Common Challenges in Managing Product Returns
While RMA processes offer many benefits, they also come with challenges:
- Handling High Volumes: Businesses need scalable systems to process large numbers of RMA requests during busy seasons.
- Ensuring Compliance: Companies must meet regional regulations for returns, especially for international shipments.
- Avoiding Fraud: Fraudulent return requests can strain resources. An RMA system reduces this risk by verifying each claim.
RMA Software: The Key to Streamlining Returns
Modern businesses rely on RMA software to handle return requests efficiently. These tools automate key tasks, including:
- Generating RMA numbers
- Providing return instructions
- Tracking shipments in real-time
- Managing reverse logistics
With RMA software, businesses improve processing speed, reduce errors, and enhance overall efficiency. Integration with PLM or ERP systems further optimizes workflows, making it easier to track returns and improve products over time.
Why RMA Matters for Customer Satisfaction
The return process is often a customer’s final interaction with a brand. A seamless RMA experience can leave a lasting impression. Here’s how:
- Reduces Frustration: Clear instructions and quick resolutions prevent negative experiences.
- Builds Trust: Customers appreciate businesses that handle returns professionally, increasing their confidence in future purchases.
- Encourages Feedback: The RMA process provides valuable insights into customer concerns, helping businesses improve.
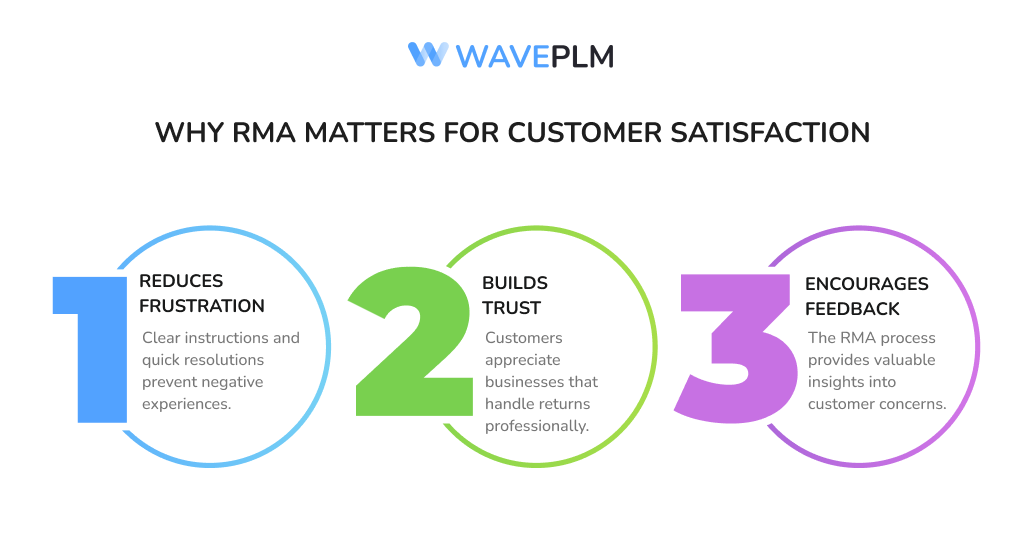
Conclusion: Why Every Business Needs an RMA System
An efficient RMA system is not optional in today’s manufacturing and shipping industries. From processing returns to improving quality control, it offers significant benefits to businesses and customers alike. By understanding the RMA def and implementing the right tools, companies can streamline the return process, enhance customer satisfaction, and drive long-term success.
When integrated with PLM software, the RMA process becomes even more powerful. Businesses gain insights that improve product quality, enhance collaboration, and reduce returns. Adopting a robust RMA system with PLM integration isn’t just a smart move—it’s essential for staying competitive.
Optimize your product returns with streamlined RMA processes and PLM software solutions today. Improve quality, save costs, and deliver better customer experiences with every step.
Leave a Reply