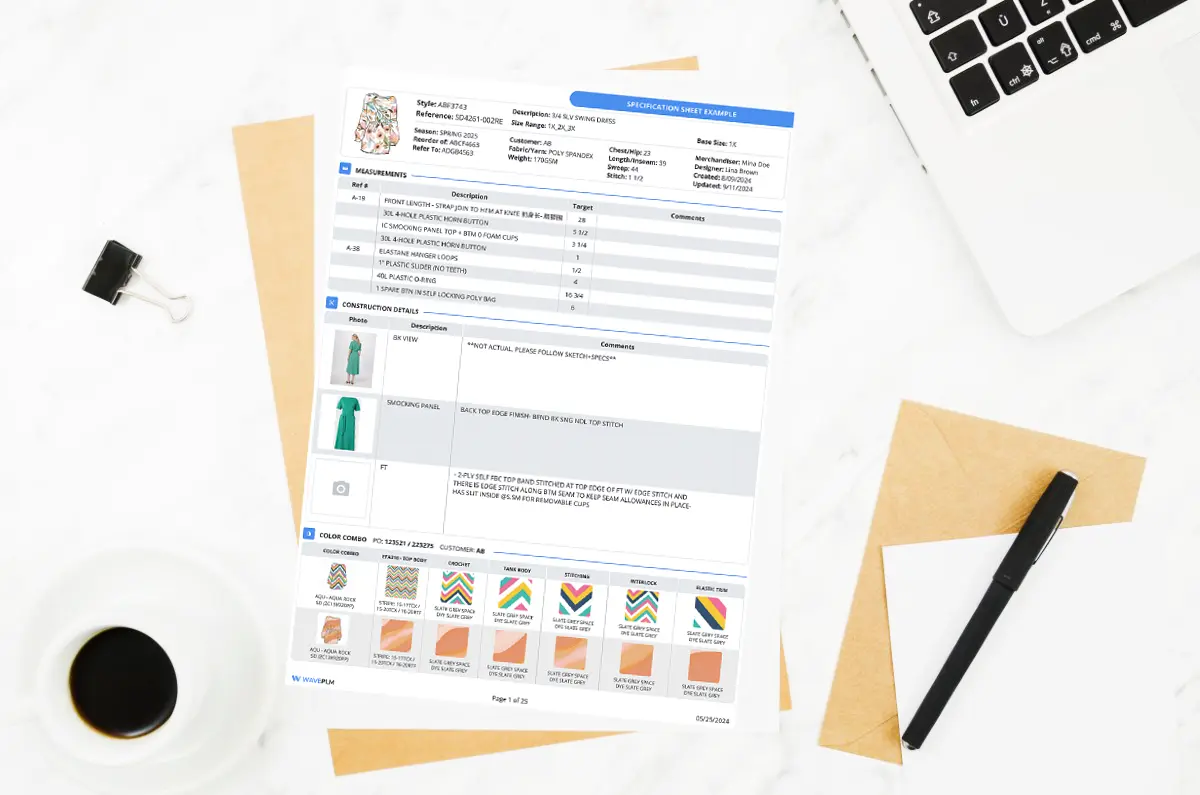
In the apparel industry, efficient production depends on clear communication and well-organized processes. A specification sheet, also known as a design specification sheet or product spec sheet, is one of the most important tools in apparel manufacturing. This document ensures that everyone involved in the production process understands the product’s design, quality standards, and manufacturing requirements.
In this guide, we’ll explore the specification sheet meaning, why it’s essential for apparel production, and how to create one that streamlines your production processes and improves customer satisfaction.
What is a Specification Sheet?
A spec sheet is a document that includes detailed product information for a garment. It outlines the design specifications, such as measurements, fabric, color, and construction details, ensuring that manufacturers and other team members have all the information needed to create a product accurately.
This document provides both written details and visual representation of the product. It eliminates guesswork and helps maintain quality throughout the manufacturing process.
Why Are Specification Sheets Important in Apparel Production?
1. Clear Communication Across Teams
A sheet specifications is a shared language for designers, manufacturers, and quality control teams. It ensures everyone is on the same page.
2. Improved Quality Control
Including quality standards and specific details in the sheet ensures that every product meets the desired specifications. This consistency enhances customer satisfaction.
3. Streamlined Production Processes
With a detailed product spec sheet, manufacturers can follow instructions easily, reducing delays and costly mistakes during the manufacturing process.
4. Enhances User Experience
When the final product aligns with the original design, it improves the user experience and builds trust with customers.
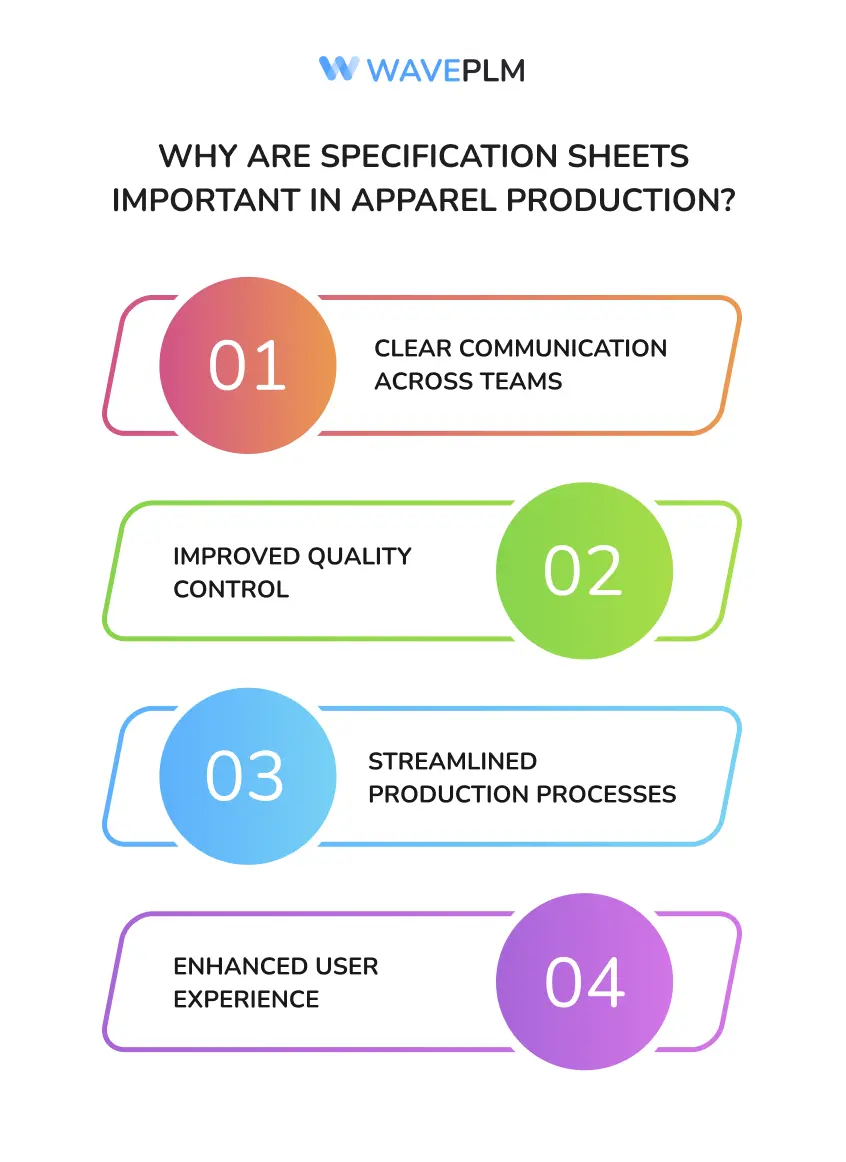
What to Include in a Specification Sheet
To create a specification sheet that’s easy to use and effective, include the following key elements:
1. Product Description and Visual Representation
Start with a clear product description. This should include the type of garment, its purpose, and any unique features. Add a visual representation, such as a sketch, photo, or digital rendering, to clarify the design further.
2. Measurements and Sizing
List detailed measurements for each part of the garment. For example, provide chest, sleeve, and length measurements. Include size ranges and tolerances to ensure precision during production.
3. Fabric and Material Specifications
Specify the type of fabric, color codes, trims, and any additional components. This section ensures the right materials are used in the production processes.
4. Construction Details
Outline the sewing methods, seam allowances, and other specific details about how the garment should be assembled.
5. Quality Standards
Define clear quality standards, such as acceptable tolerances for measurements, stitching requirements, and fabric quality.
6. Additional Information
Include any other additional information needed for production, such as washing instructions, packaging details, or special labels.
How to Write a Specification Sheet
Writing a specification sheet is about presenting specific details in a way that’s easy for your team members to follow. Here’s how to do it:
Step 1: Understand the Product
Before writing, gather all relevant product information. This includes design sketches, fabric details, and the intended purpose of the garment.
Step 2: Use Simple and Clear Language
Avoid complex terms unless necessary. Write in a way that ensures everyone, from designers to manufacturers, can easily understand the instructions.
Step 3: Organize Information Logically
Group similar details together. For example, keep all measurement information in one section and fabric details in another.
Step 4: Include Visual Representation
Visual aids, such as diagrams or sketches, make it easier for manufacturers to understand the design specifications.
Step 5: Focus on Quality Standards
Add checkpoints for quality control. For example, specify the tolerance for measurements or fabric weight to maintain consistency.
Step 6: Collaborate with Your Team Members
Get feedback from designers, manufacturers, and project managers. This ensures your specification sheet covers all necessary specific details.
How Specification Sheets Help in Apparel Production
A well-written design specification sheet provides many benefits in the manufacturing process:
1. Fewer Errors During Production
Clear design specifications eliminate confusion. Manufacturers can follow the instructions accurately, reducing errors and ensuring the product matches the designer’s vision.
2. Faster Production
With clear instructions, manufacturers don’t need to ask for clarifications. This speeds up the production processes and saves time.
3. Better Quality Products
Including quality standards in the spec sheet ensures consistency across all products. This attention to detail improves customer satisfaction.
4. Enhanced Customer Satisfaction
When the product meets customer expectations, it builds trust and loyalty. A well-executed product also improves the overall user experience.
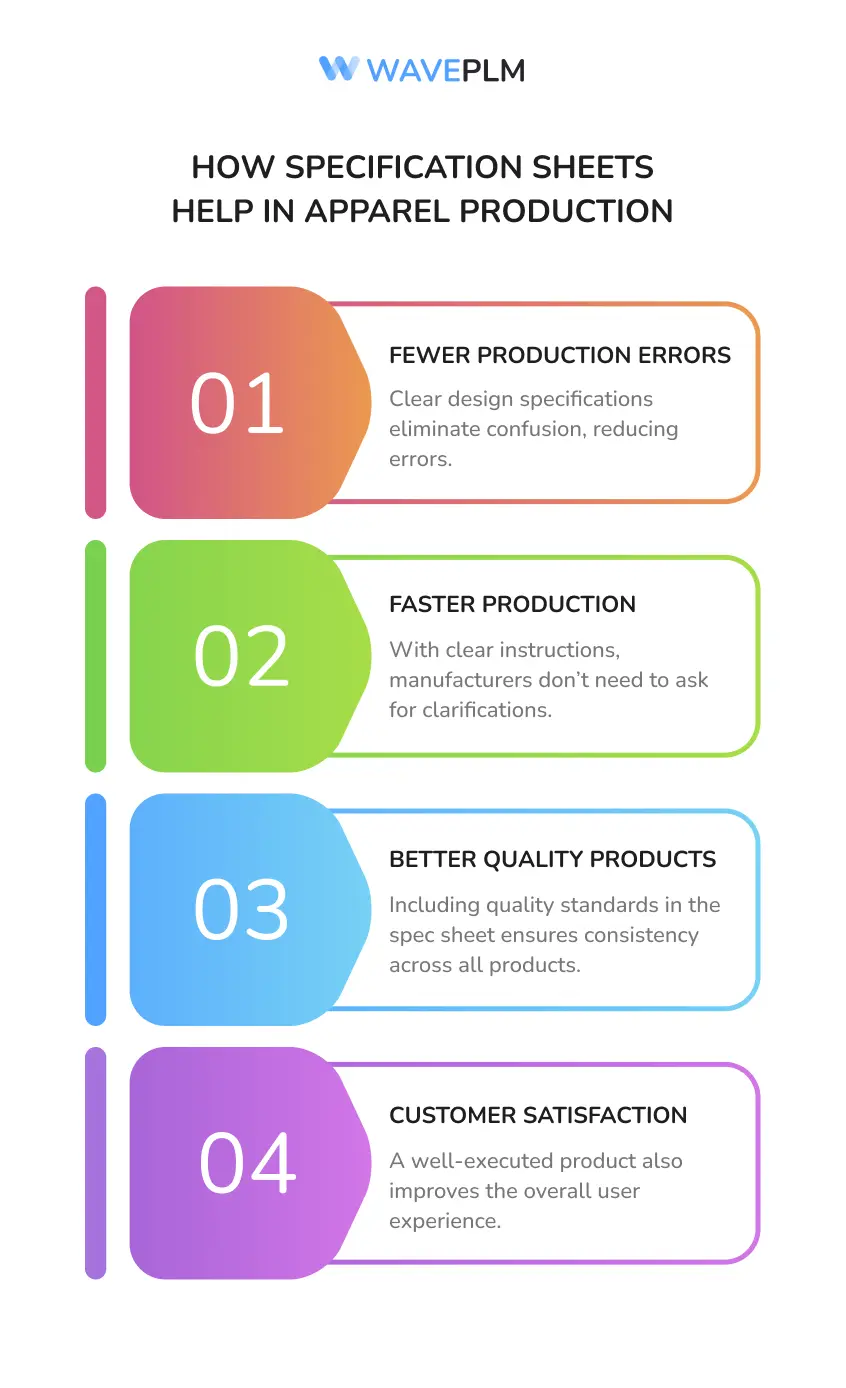
Common Mistakes to Avoid
1. Leaving Out Important Information
Missing key details can cause errors during production. Always double-check your specification sheet to ensure it includes all the necessary design specifications.
2. Using Complicated Language
Overly technical terms can confuse manufacturers. Use simple, clear language to describe the product information.
3. Neglecting Quality Standards
Without clear quality control measures, products may vary in quality. This inconsistency can hurt your brand’s reputation.
4. Overloading with Unnecessary Information
Avoid overwhelming your team members with too much information. Focus on the specific details that directly impact the manufacturing process.
Can PLM Software Replace Specification Sheets?
While spec sheets are essential for apparel production, they are not without limitations. Paper-based or standalone digital spec sheets can be prone to miscommunication, errors, and delays in updating information. Modern PLM (Product Lifecycle Management) software offers a powerful alternative to traditional spec sheets.
Here’s how PLM software can replace and enhance the functionality of a specification sheet:
1. Centralized Product Information
PLM systems acts as a single source of truth for all product information. It allows design teams, project managers, and manufacturers to access and update data in real time, eliminating version control issues.
2. Visual Representation and Design Specs
Like a spec sheet, fashion PLM systems include tools for visual representation and storing design specifications. However, it enhances these features with 3D design tools, version tracking, and instant sharing capabilities.
3. Real-Time Collaboration
PLM software allow seamless collaboration among team members, regardless of location. Designers, manufacturers, and quality control teams can access and update specific details simultaneously, ensuring everyone stays aligned.
4. Integrated Quality Control
Unlike static spec sheets, PLM software includes built-in quality control features. Teams can define quality standards, track compliance, and resolve issues within the platform.
5. Faster Updates
Making changes to a traditional spec sheet can be time-consuming. With apparel PLM, updates are instant, ensuring the latest design specifications are always available during the manufacturing process.
6. Improved Efficiency and Reduced Costs
By automating many aspects of creating and sharing product data, PLM software reduces manual work, speeds up the production processes, and lowers costs.
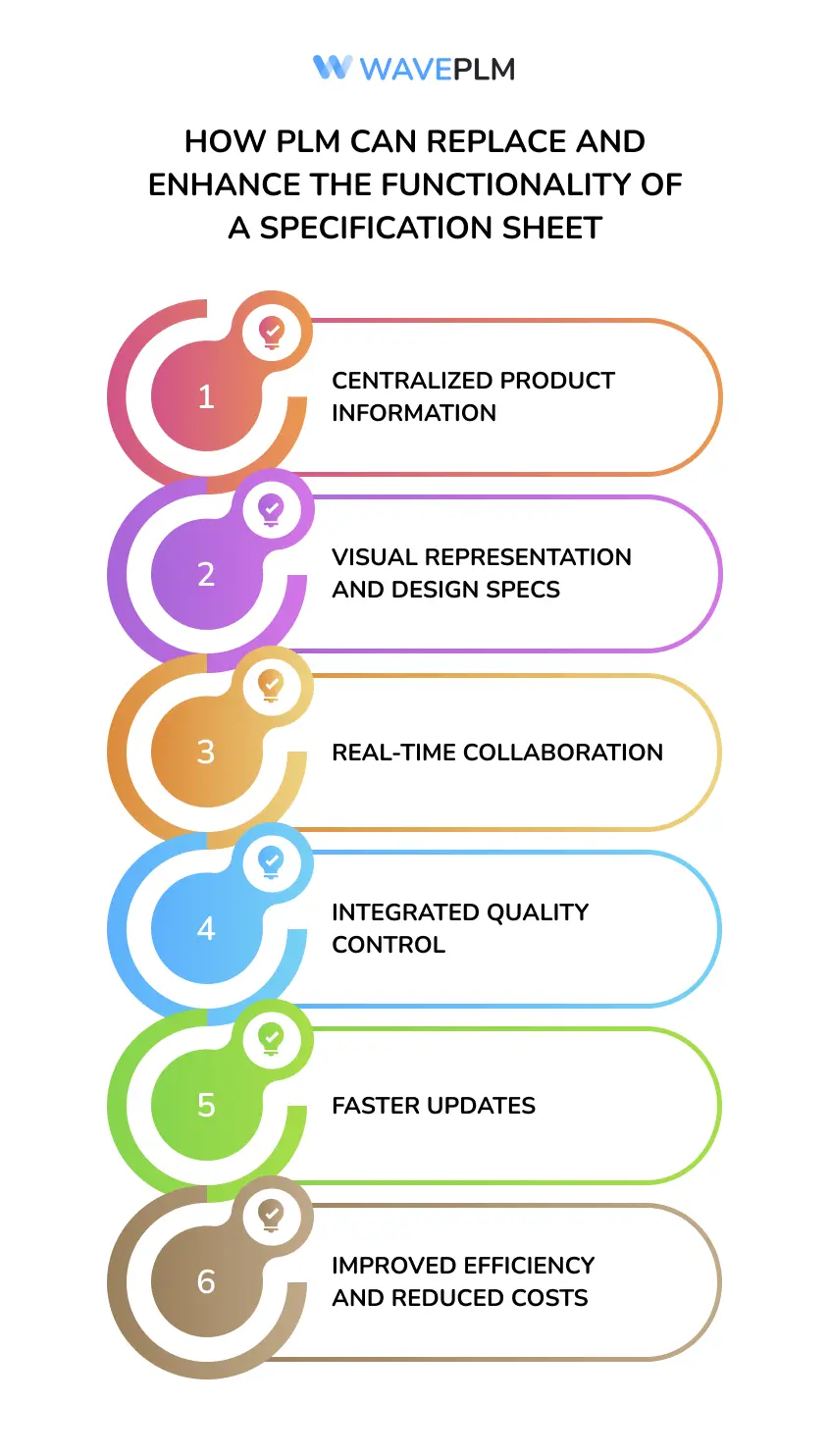
Why Choose PLM Software Over Traditional Specification Sheets?
Using PLM systems to manage design specifications and production processes helps businesses stay competitive in today’s fast-paced fashion industry. It eliminates the need for multiple tools by integrating product design, manufacturing, and quality control into one streamlined system.
For teams looking to modernize their approach, fashion PLM software offers everything a traditional specification sheet does—and more. It’s the future of efficient apparel production and a must-have for brands that value accuracy, speed, and customer satisfaction.
Switching to Wave PLM can transform how you understand the product, collaborate across teams, and deliver exceptional results.
Leave a Reply