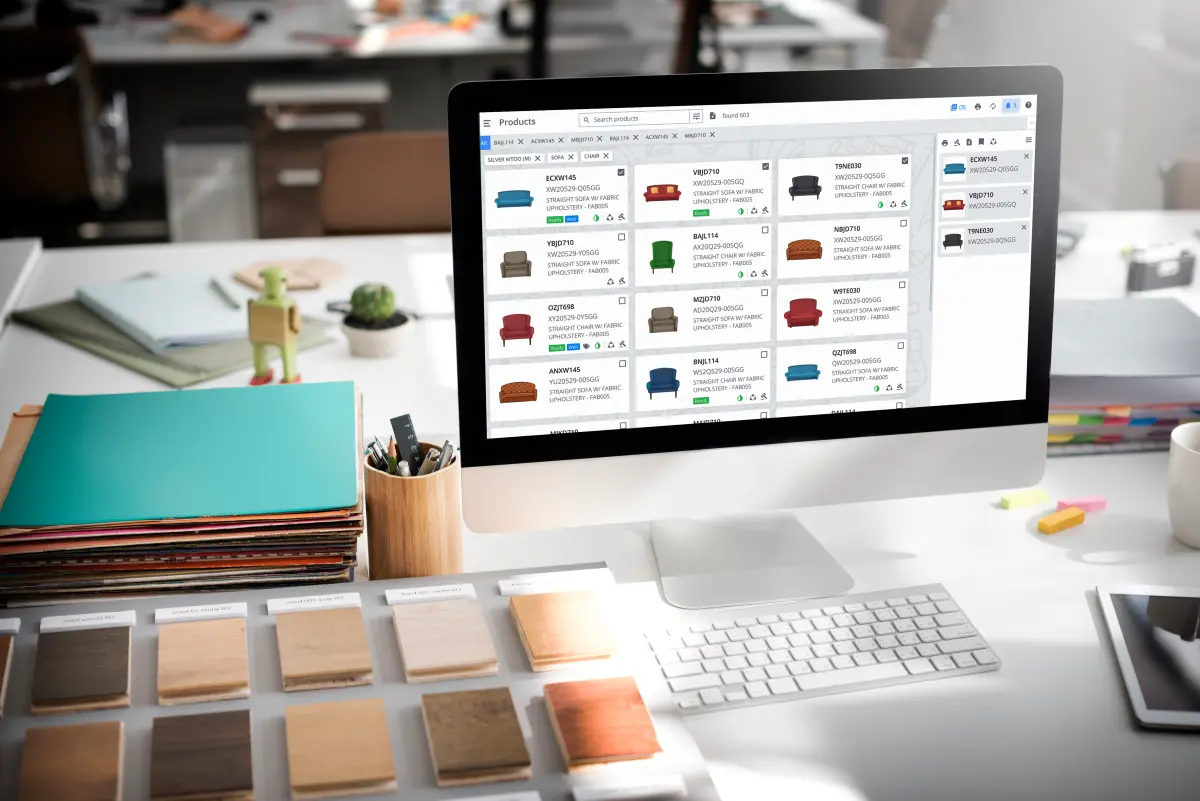
The home decor market is competitive. Consumers want stylish, high-quality products that blend design with functionality. Brands must balance aesthetics with practicality while maintaining efficient production processes.
This is where PLM software plays a crucial role. It streamlines product development, integrates furniture-building software, and enhances product design to create innovative home decor furnishing solutions.
The Role of PLM Software in Home Material Decor
PLM software transforms the way brands approach home material decor. It centralizes data, ensuring that every stage of the product lifecycle is efficient. From concept to production planning, PLM helps product managers, designers, and manufacturers collaborate seamlessly.
This cross-functional integration reduces errors, improves product quality, and speeds up time to market. It also ensures that teams have access to up-to-date information, reducing confusion and miscommunication across departments.
One of the major advantages of PLM tools is its ability to connect every stage of the product development cycle. From ideation and prototyping to sourcing materials and final production, PLM keeps all aspects organized. With this level of control, brands can ensure that every detail aligns with the final vision of the product, making home decor furnishing more efficient and streamlined.
Enhancing Product Development and Design
PLM software optimizes product development by enabling teams to manage specifications, materials, and designs in one platform. It integrates with furniture design software and computer-aided design (CAD) tools, allowing designers to create and modify products effortlessly. These features help brands stay ahead of trends and meet customer expectations for home decor furnishing.
3D modeling capabilities further enhance product design. Designers can visualize how a product will look and function in real-world settings. This eliminates costly mistakes and ensures that products meet both aesthetic and functional requirements. By incorporating user feedback during early design stages, brands can refine their offerings and improve customer satisfaction.
With digital prototyping, teams can test different design concepts before physical production begins. This capability not only improves accuracy but also reduces material waste and unnecessary production expenses. By leveraging virtual design tools, brands can experiment with colors, textures, and materials to create the best possible home decor furnishing solutions.
Improving Production Planning and Reducing Costs
Effective production planning is essential for maintaining profitability in the home decor industry. PLM systems connect design and manufacturing teams, ensuring that materials, costs, and schedules align. With an integrated bill of materials (BOM) management system, brands can track components and materials, reducing waste and optimizing resource allocation.
PLM software also identifies supply chain inefficiencies. By analyzing production workflows, companies can eliminate bottlenecks and streamline processes. This results in faster production cycles, lower costs, and a more competitive advantage in the market.
One of the biggest challenges in home decor manufacturing is managing multiple suppliers for different materials. PLM software makes it easier to oversee procurement by tracking supply chain progress and automatically updating teams about changes in availability. This ensures that production planning stays on track, preventing costly delays and inventory shortages.
Additionally, PLM software helps reduce excess inventory by enabling better forecasting and demand planning. Brands can produce only what is needed, minimizing waste while optimizing production resources. This results in significant cost savings and a more sustainable approach to home material decor manufacturing.
Addressing Industry Pain Points with PLM Software
Brands in the home decor sector face challenges such as high material costs, design revisions, and supply chain disruptions. PLM provides solutions by offering:
- Real-time data access to track inventory, production status, and design updates.
- Automated workflows that reduce manual errors and improve efficiency.
- Collaboration tools that enhance communication among design, engineering, and production teams.
- Quality control features that ensure products meet industry standards and customer expectations.
By addressing these pain points, PLM software enables brands to focus on innovation rather than operational inefficiencies.
Another major issue in home decor production is ensuring compliance with safety and sustainability standards. PLM software simplifies compliance management by maintaining records of materials used, safety tests conducted, and certifications required. This ensures that all home decor furnishing products meet regulatory standards without unnecessary delays or complications.
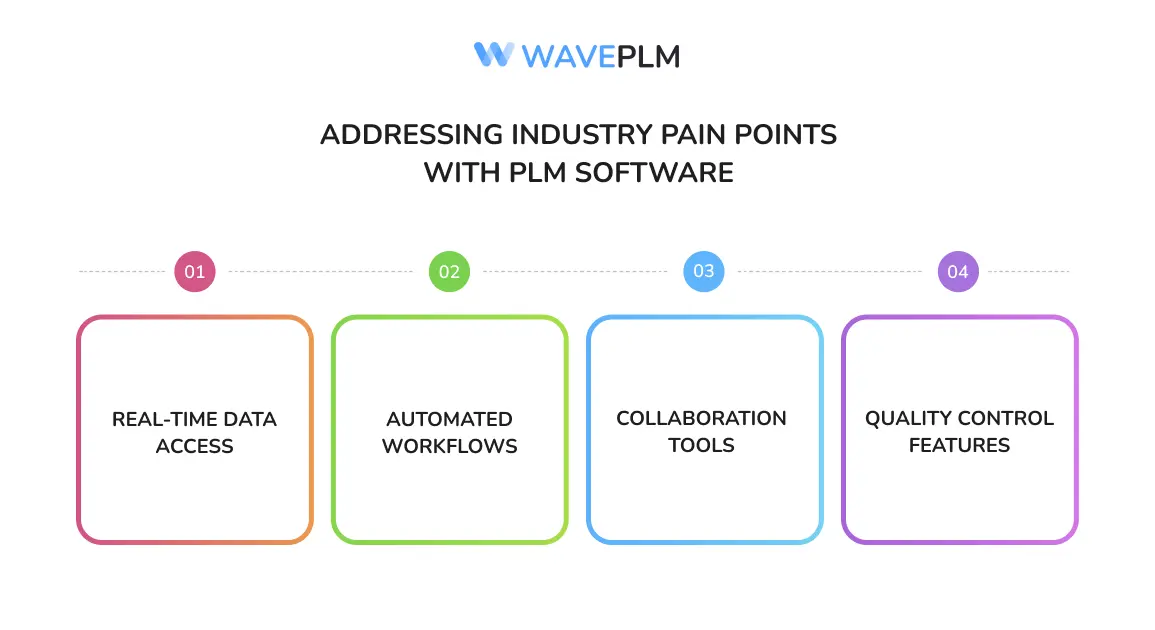
Gaining a Competitive Advantage with PLM
Incorporating PLM software into furniture building software enhances a company’s ability to produce high-quality home material decor. It allows businesses to:
- Reduce costs by optimizing material usage and production processes.
- Improve product functionality with better design and engineering collaboration.
- Streamline project management by centralizing data and workflows.
- Increase customer satisfaction by delivering well-designed, high-quality products faster.
Brands that leverage PLM software gain an edge in the competitive home decor market. They can bring products to market more efficiently while maintaining high design and quality standards.
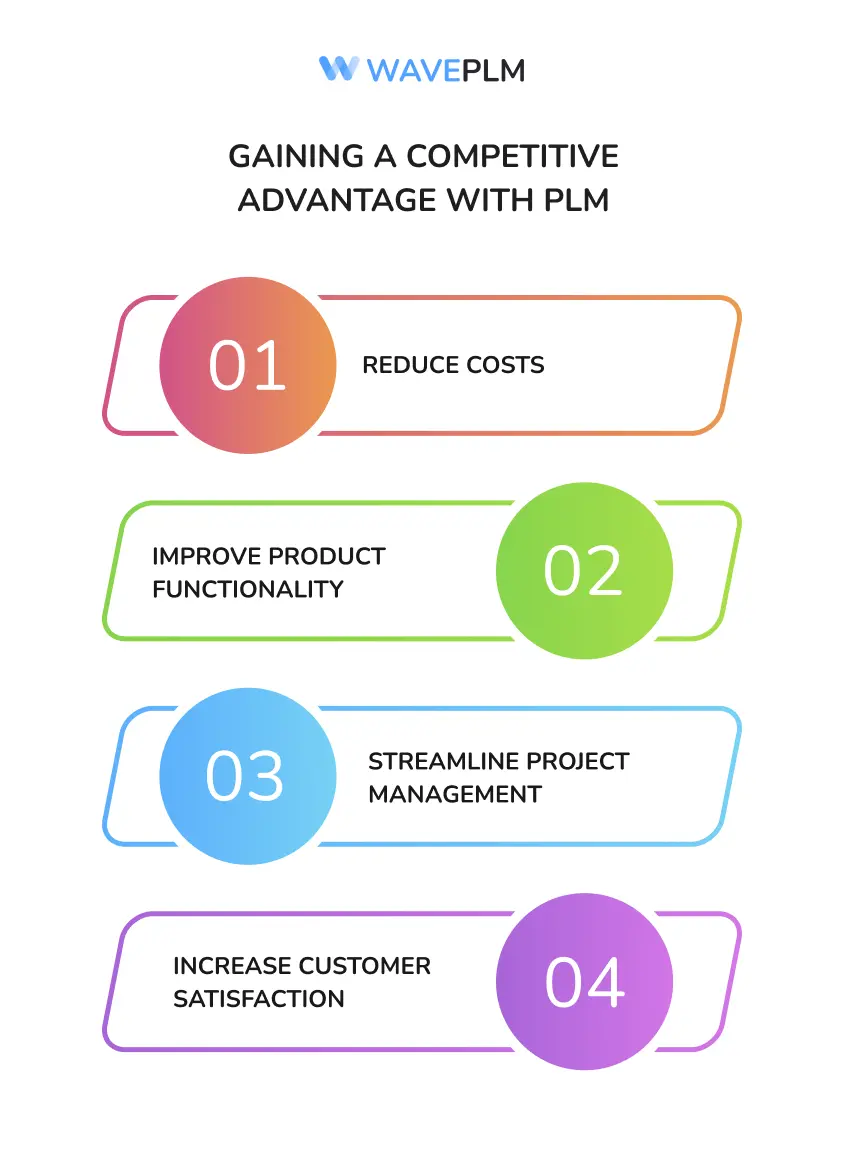
Furthermore, companies using PLM software can benefit from advanced analytics. By evaluating production data and market trends, brands can make data-driven decisions that enhance product design and marketing strategies. This level of insight ensures that businesses stay ahead of customer demands and consistently deliver top-tier home decor furnishing solutions.
Try PLM Software with a Free Trial
For brands looking to improve their product development process, a free trial of PLM software can demonstrate its value. By testing features like 3D modeling, BOM management, and supply chain integration, businesses can see firsthand how PLM enhances efficiency and innovation in home decor furnishing.
Companies hesitant to implement new technology can start with a free trial to explore the software’s capabilities. They can evaluate how well it integrates with their existing systems, assess usability for their teams, and determine its impact on productivity. This hands-on experience helps brands make informed decisions before committing to full-scale adoption.
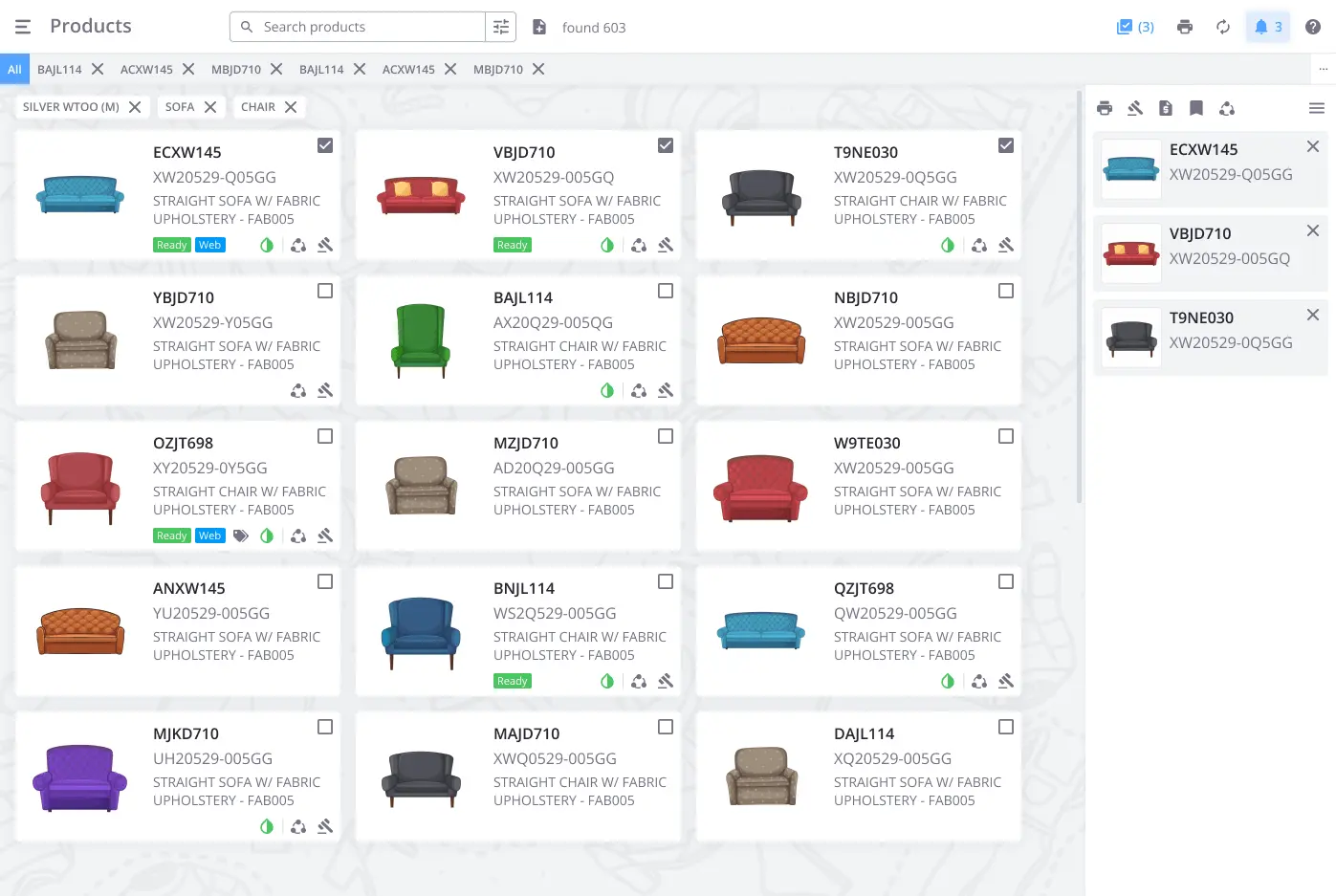
Conclusion
PLM systems bridge the gap between design and functionality in home material decor. It streamlines product development, improves production planning, and reduces costs while enhancing customer satisfaction.
By connecting PLM with furniture design software and other digital tools, brands can stay competitive. This helps them create high-quality and stylish home decor products. If you want to improve your processes, try Wave PLM software with a free trial. This is a step toward success.
As consumer demands evolve, businesses must continuously improve their product offerings. PLM software enables brands to achieve this by fostering innovation, enhancing operational efficiency, and improving collaboration across departments. PLM is a key tool for success in the home decor industry. It helps with both small projects and large manufacturing.
Leave a Reply