Quality control is an essential aspect of any manufacturing process, and this is especially true in the fashion industry. With the constant demand for new styles and trends, fashion manufacturers must ensure that their products are of the highest quality.
Poor quality can tarnish a brand’s reputation and lead to financial losses. Quality control is essential in ensuring that products meet the expected standards and are safe for use. It involves testing and inspecting products at every stage of the manufacturing process to identify any defects or issues that need to be addressed.
To mitigate these risks, fashion manufacturers are turning to Product Lifecycle Management (PLM) software systems for efficient quality control integration.
PLM is a software system that manages the entire lifecycle of a product, from concept to disposal. It is an essential tool for fashion manufacturers, and fashion PLM integration into quality control practices can significantly improve the manufacturing process.
Understanding PLM Integration
At its core, PLM is a software solution designed to manage the entire lifecycle of a product. It is one system that serves as a centralized hub where all relevant product data, including design files, specifications, materials, and production schedules, can be stored, accessed, and updated by various stakeholders throughout the supply chain.
PLM integration involves linking PLM systems with other critical business processes, such as other enterprise systems such as quality control, inventory management, and supply chain logistics. This integration allows for real-time data sharing and collaboration, enabling more efficient decision-making and problem-solving.
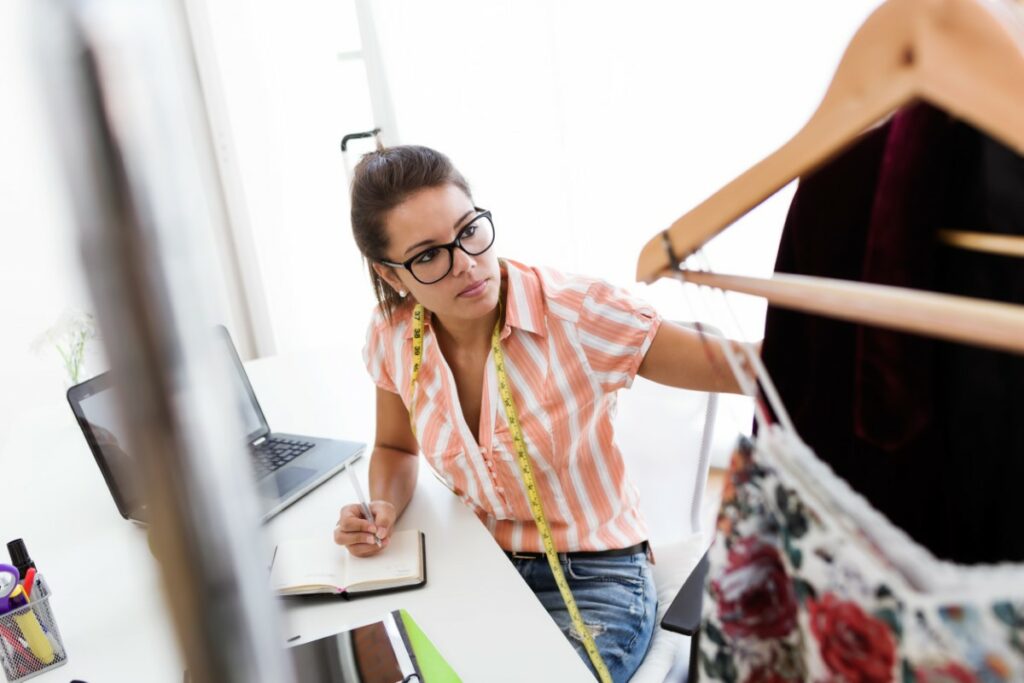
The Role of PLM in Quality Control
Quality control is a multifaceted aspect of fashion manufacturing encompassing various production process stages, from design validation to final product inspection. PLM integration enhances quality control efforts by providing greater visibility and control over every aspect of the product development process and manufacturing.
1. Design and Development Phase
Design Validation
PLM systems enable designers to create digital prototypes and conduct virtual fittings. This allows for early validation of design concepts, ensuring that products meet aesthetic and functional requirements. Quality control parameters are integrated into the design validation process. It ensures that potential quality issues are identified and addressed before production begins.
Material Selection and Specification
During the design phase, PLM systems facilitate the selection and specification of materials. Integration with quality control protocols ensures that materials meet predefined quality standards and regulatory requirements. Real-time access to material data, including certifications and supplier information, enables informed decision-making and risk mitigation strategies.
2. Production Phase
Manufacturing Process Monitoring
PLM integration gives quality control teams real-time visibility into production workflows. They can monitor key performance indicators (KPIs) like defect rates, production yield, and lead times. Quality control sensors and automation technologies are part of the production process. It allows proactive detection of deviations from quality standards and triggering immediate corrective actions.
Compliance Assurance
PLM systems streamline compliance management by centralizing documentation, automating audit trails, using data management capabilities and facilitating communication with regulatory bodies and certification agencies. Quality control parameters are embedded into production processes to ensure adherence to safety, environmental, and labour standards throughout the manufacturing process.
3. Post-Production Phase
Quality Inspection and Testing
PLM systems help conduct quality inspections and testing after production to ensure product quality and compliance. They integrate enterprise systems with quality control protocols, allowing systematic inspection of finished products, raw materials, and components. The PLM system captures and analyzes test results, offering actionable insights for continuous improvement and quality assurance.
Feedback Loop and Continuous Improvement
PLM integration enables a closed-loop feedback system, where quality control data and customer satisfaction insights are fed back into the product development and manufacturing processes. Lessons learned from quality issues and customer feedback drive continuous improvement initiatives, ensuring that quality standards are continuously refined and upheld across product lifecycles.
4. Compliance Assurance
In the highly regulated fashion industry, compliance with safety, environmental, and labour standards is non-negotiable. PLM integration streamlines compliance management by centralizing documentation, automating audit trails, and facilitating communication with regulatory bodies and certification agencies. By ensuring adherence to standards throughout the product lifecycle, manufacturers can mitigate risks and protect their brand reputation.
Benefits of PLM Integration for Quality Control
The integration of PLM systems into quality control processes offers numerous benefits for fashion manufacturers:
Improved Collaboration
Effective collaboration is essential for efficient product development, ensuring that quality standards are met throughout the product development and manufacturing process. PLM integration facilitates collaboration by providing a centralized platform where all stakeholders can access, share, and update relevant information in real time. Designers can collaborate with manufacturers to ensure that product designs meet production feasibility requirements, while quality control specialists can work closely with production teams to identify and address potential quality issues before they escalate.
Moreover, PLM integration enables seamless communication and transparency across departments and organizational boundaries. With all product-related data and workflows accessible from a single source of truth, teams can collaborate more effectively, make informed decisions, and resolve issues proactively. By breaking down silos and fostering a culture of collaboration, PLM integration strengthens the business operations overall quality control process and enhances organizational agility.
Enhanced Efficiency
Efficiency is crucial for meeting quality control objectives while minimizing time and resource constraints. PLM integration improves efficiency by automating repetitive tasks, streamlining workflows, and eliminating manual data entry errors. For example, by integrating PLM systems with quality control sensors and automation technologies, manufacturers can have streamlined workflows that automate data collection, analysis, and reporting, reducing the time and effort required for manual inspections and audits.
Furthermore, PLM integration enables better enterprise resource planning, allocation and utilization by providing real-time visibility into production processes and performance metrics. Quality control teams can identify bottlenecks, optimize production workflows, and allocate resources more effectively to meet quality targets and production deadlines. By reducing unnecessary delays and inefficiencies, PLM integration maximizes operational efficiency and enhances overall productivity.
Faster Time-to-Market
In today’s fast-paced fashion industry, speed is of the essence. PLM integration accelerates time-to-market by streamlining product development processes and cycles, minimizing rework, and reducing time-consuming manual interventions. By digitizing and automating design validation, material sourcing, and production planning processes, manufacturers can shorten lead times and bring high-quality products to market faster.
Moreover, PLM integration enables faster decision-making by providing real-time, accurate data, insights and analytics. Quality control teams can quickly identify and address quality issues, make informed decisions about product design changes or manufacturing processes, and implement corrective actions without delay. By reducing time-to-market, PLM integration enables fashion companies to capitalize on market opportunities, respond to consumer trends, and stay ahead of competitors in an increasingly dynamic industry landscape.
Cost Savings
Effective quality control is not only essential for product quality but also for cost management. PLM integration helps fashion manufacturers reduce costs associated with poor quality, scrap, rework, and inventory management inefficiencies. By minimizing quality defects and production errors, manufacturers can reduce the need for costly rework and warranty claims, thereby lowering overall production costs.
Additionally, PLM integration enables better inventory management by providing real-time visibility into material availability, usage, and replenishment requirements. By optimizing inventory levels and reducing excess stock, manufacturers can minimize inventory holding costs and improve cash flow. Moreover, by enabling data-driven decision-making and process optimization, PLM integration supports strategic cost management initiatives, helping fashion companies achieve sustainable profitability in a competitive market environment.
Conclusion
In conclusion, PLM integration offers numerous benefits for quality control in fashion manufacturing, including improved collaboration, enhanced efficiency, faster time-to-market, and cost savings. PLM systems help fashion companies by organizing product data, simplifying workflows, managing customer relationships, and improving communication across the supply chain. As a result, this enables them to meet consumer demands, adhere to regulations, and outperform competitors. As the industry continues to evolve, embracing PLM integration will be essential for driving innovation, improving operational excellence, and delivering value to customers in a rapidly changing market landscape.
PLM integration can also improve communication between different departments involved in the manufacturing process. With PLM, designers, manufacturers, and quality control teams can all work together in a single system. This allows for better collaboration and communication, reducing the risk of miscommunication and errors.
In addition to improving quality control processes, PLM integration can also help manufacturers improve their overall product quality. By tracking every aspect of the product lifecycle, manufacturers can identify areas where improvements can be made. For example, PLM-integrated systems can help manufacturers identify production defects and the most common mistakes.
Moreover, Wave PLM has a special product for use in quality control in production – QC App. It helps to resolve issues early in the production stage and provides you instant access for the QC team to all info and the ability to enter inspection results on site. Now you can try all Wave PLM benefits with a three-month free trial. Don’t miss the chance to improve the quality of your production.
Leave a Reply