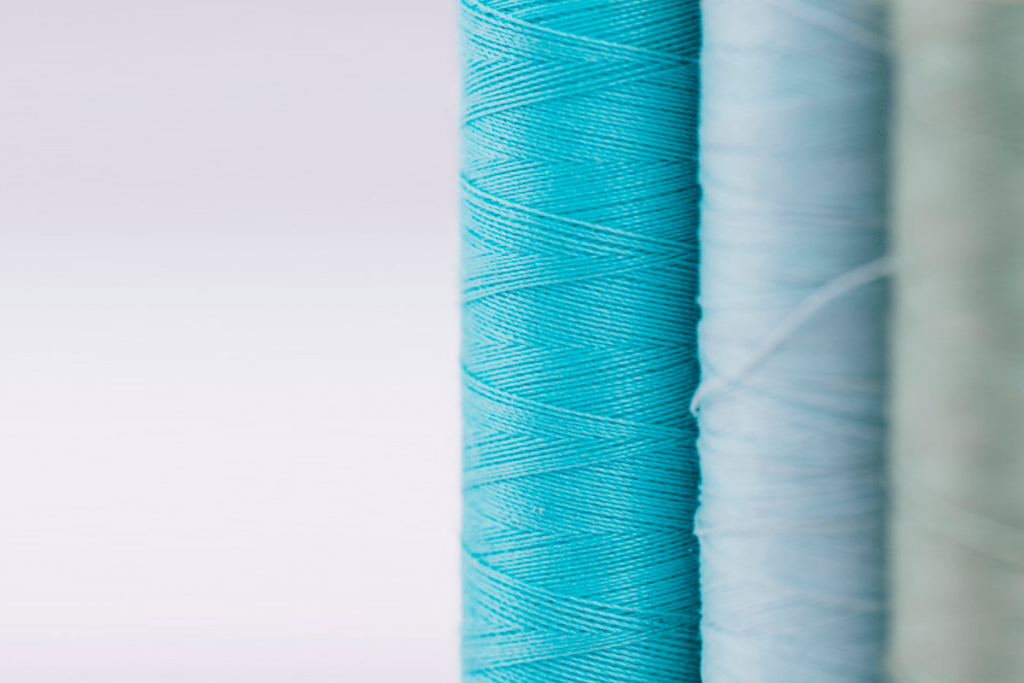
The textile manufacturing industry, a linchpin of the global economy, this huge and diverse industry has traversed a rich tapestry of evolution over centuries, adapting to technological advancements, societal shifts, and the ever-changing demands of fashion and functionality.
While the final products – the garments and fabrics that adorn our daily lives – might appear deceptively simple, the intricate processes involved in textile manufacturing weave a complex and fascinating narrative. This comprehensive exploration delves beyond the threads. It unravels the multifaceted stages, technological intricacies, and challenges that define the vibrant landscape of textile manufacturing.
The Journey of Fibers: From Raw Materials
At the genesis of textile creation lies the selection and transformation of raw materials, with natural fibers such as cotton, wool, and silk, or their synthetic counterparts like polyester and nylon. This stage sets the foundation for the entire manufacturing process, encompassing meticulous processes like harvesting wet processing, cleaning, and spinning. Each fiber type and spinning technique employed during this crucial stage significantly influences the characteristics of the final textile product.
Natural fibers, sourced from plants, animals, or minerals, bring a unique set of qualities to the textile landscape. Cotton fabric, the most widely used natural fiber, boasts breathability and comfort, making it a staple in the production of everyday fabrics. Wool, renowned for its warmth and insulation properties, finds its place in winter garments. Luxurious silk, with its smooth texture and natural sheen, graces high-end fashion pieces. Additionally, innovations in the extraction and processing of fibers from unconventional sources, such as bamboo and seaweed, showcase the textile manufacturing industry’s commitment to sustainability and resource diversification.
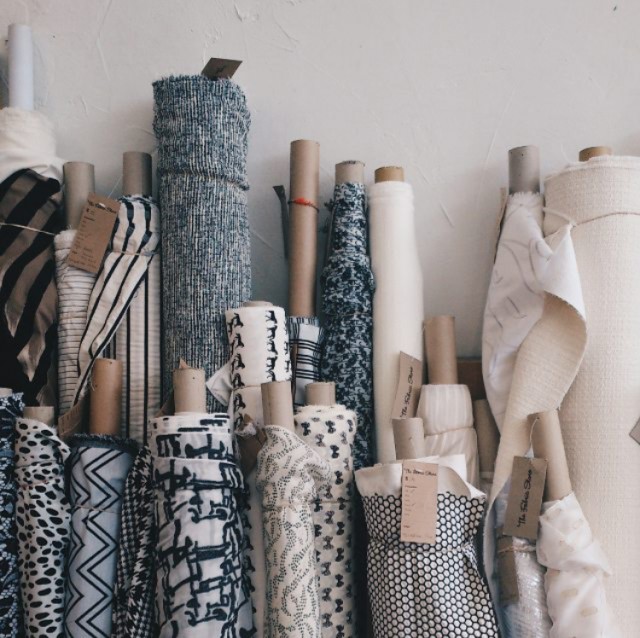
On the other synthetic fibres front, polymers like polyester and nylon dominate the landscape. Polyester, with its durability and resistance to wrinkles, is a go-to choice for activewear and outdoor gear. Nylon, recognized for its strength and abrasion resistance, often finds its place in hosiery and sportswear. The ongoing exploration of biodegradable synthetic fibers exemplifies the textile industry’s continuous quest for environmentally friendly alternatives.
The Transformation from Raw Fibers to Yarns
The transformation from raw fibers to yarns involves a meticulous dance of machinery raw materials inventory and craftsmanship. The spinning process, historically a manual endeavor, has witnessed a technological revolution with the advent of automated spinning machines, enhancing efficiency and output. These machines, often computer-controlled, ensure consistent yarn quality, finer textures, and increased production rates. As the yarns take shape, they set the stage for the subsequent intricate stages of the textile manufacturing process.
The journey of fibers represents the foundational chapter in the textile manufacturing saga. The selection of raw materials, the spinning and weaving processes, and the infusion of innovation set the tone for the subsequent chapters, where these yarns metamorphose into the diverse and versatile fabrics that define our clothing and surroundings. In the following sections, we will unravel the intricacies of weaving and knitting. We will also delve into the artistry of dyeing and finishing, explore the transformative impact of automation and Industry 4.0, and confront the challenges while championing sustainability in the ever-evolving landscape of modern textile manufacturing itself.
Weaving and Knitting: Earliest Textile Manufacturing Process
Having traversed the foundational journey of fibers, the narrative of earliest textile manufacturing process unfolds further as yarns transition into fabrics through the age-old crafts of weaving and knitting. These techniques, with roots dating back more than a quarter millennia, have not only survived the test of time but have evolved into sophisticated processes that contribute to the diverse and dynamic nature of textiles.
Weaving, a methodical interlacing of horizontal (weft) and vertical (warp) yarns, forms the backbone of structured fabrics. The loom, an iconic apparatus in weaving, operates as a canvas for intricate patterns and designs. Traditional handlooms, once the cornerstone of many textile industries’ production processes, have given way to modern power looms and automated weaving machines. These technological marvels not only expedite the weaving process. It also allow for greater precision in creating complex patterns and textures.
The intricate dance of warp and weft threads not only determines the visual appeal of the fabric but also influences its strength and durability. Various weaving patterns, such as plain weave, twill, and satin, contribute distinct characteristics to the final textile. Twill weaves, characterized by diagonal lines, offer increased durability and flexibility, making them suitable for denim fabrics. Satin weaves, with their smooth and lustrous finish, are favored in high-end garments.
The Art of Knitting
In contrast, the art of knitting involves the creation of fabric by interlocking loops of yarn. This technique, often associated with the creation of stretchable and flexible textiles, has found prominence in the production of hosiery, sweaters, and other garments that require elasticity. Knitting machines, whether manual or computerized, have significantly advanced the efficiency and complexity of the knitting process. Circular knitting machines, for instance, produce seamless tubes of fabric, minimizing waste and enhancing comfort in the final product.
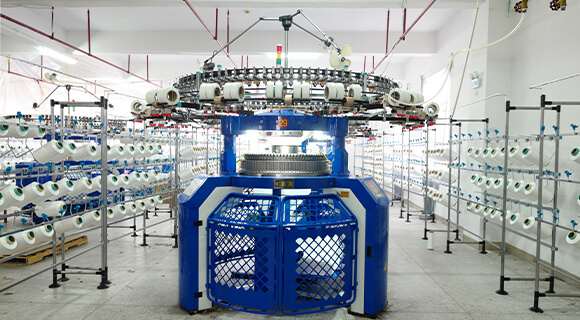
The choice between weaving and knitting is not merely an aesthetic decision; it dictates the fabric’s inherent qualities and applications. Weaving yields fabrics with a structured and stable character, while knitting produces textiles with inherent stretch and drape. The evolution of these techniques showcases the textile manufacturing industry’s adaptability and commitment to meeting diverse consumer needs.
Dyeing and Finishing
With fabrics taking form through weaving or knitting, the next pivotal stage in textile manufacturing involves the infusion of color through dyeing. Beyond the aesthetic appeal, advancements in dyeing technologies are steering the industry toward more sustainable and eco-friendly practices.
Dyeing processes traditionally involved the use of water-intensive methods and a spectrum of chemicals. However, the textile industry is undergoing a paradigm shift towards more sustainable alternatives. Waterless dyeing technologies, such as air dyeing and digital printing, are gaining traction, significantly reducing water consumption and chemical waste. Additionally, the development of plant-based and bio-degradable dyes aligns with the growing demand for eco-conscious textiles.
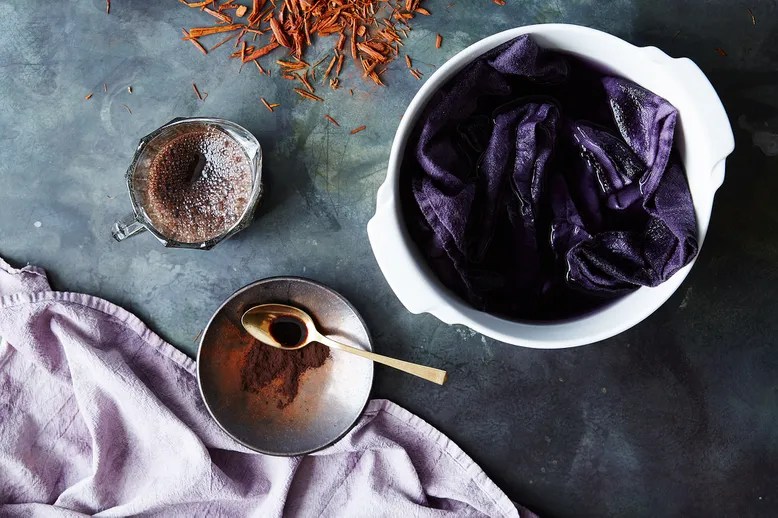
Post-dyeing, the fabric undergoes a series of finishing processes to enhance its properties. Finishing serves not only aesthetic purposes but also functional ones. Processes such as calendaring, which involves passing the fabric through heated rollers, impart a smooth finish and enhance durability. Mercerization, a treatment for the cotton industry, improves fabric’s lustre, strength, and dye affinity. Meanwhile, advancements in nanotechnology have opened up new frontiers. It allows for the creation of fabrics with enhanced properties, such as stain resistance and moisture-wicking capabilities.
The intricate interplay between the dyeing process and finishing stages ensures that the final textile product not only meets aesthetic expectations but also aligns with functional requirements. As the industry evolves, the emphasis on sustainable dyeing practices and eco-friendly finishing techniques continues to shape the future of textile manufacturing.
Automation and Industry 4.0 in Textile Manufacturing
As the textile industry continues its journey from raw materials to produce yarn to finished fabrics, the advent of automation and the principles of Industry 4.0 have ushered in a new era of efficiency, precision, and innovation in textile manufacture. From automated looms to robotic sewing machines, the integration of cutting-edge technologies is transforming traditional manufacturing and shaping the future of textile production processes.
Automated looms represent a pivotal evolution in weaving technology. Controlled by computer systems, these looms allow for intricate and complex patterns with unmatched precision. The automation of the weaving process not only accelerates production rates but also ensures consistency in fabric quality. The ability to program these machines with intricate designs opens avenues for creative expression, enabling the production of fabrics with diverse textures and patterns.
Similarly, robotic sewing machines have revolutionized the assembly of garments. These machines, equipped with advanced sensors and programming, offer unparalleled speed and accuracy in stitching. The precision afforded by robotic sewing not only reduces the margin of error but also enhances the overall quality of the final product. Additionally, the integration of artificial intelligence (AI) allows these machines to adapt to different fabrics and patterns. It further streamlines the textile manufacturing process.
The rise of smart production lines, guided by data analytics and machine learning algorithms, marks a fundamental shift in how textiles are manufactured. Real-time monitoring of production metrics, predictive maintenance, and quality control are now facilitated by interconnected systems. This not only ensures operational efficiency but also minimizes waste and optimizes resource utilization. The adoption of Industry 4.0 principles positions the textile industry at the forefront of the Fourth Industrial Revolution, fostering a more agile and responsive manufacturing ecosystem.
Benefits of Industry 4.0
The infusion of automation and Industry 4.0 principles into textile manufacturing is a transformative journey that extends beyond the weaving and sewing stages, touching every aspect of production progress. The integration of advanced technologies not only enhances efficiency but also fosters a more agile, data-driven, and interconnected textile manufacturing brand and ecosystem.
- Supply Chain Integration. Industry 4.0 facilitates a seamless integration of the entire supply chain, from raw material sourcing to product distribution. Smart sensors and data analytics enable real-time tracking of inventory levels, ensuring that production aligns with demand. This interconnectedness optimizes resource utilization, minimizes excess stock, and reduces lead times.
- Predictive Maintenance. One of the notable advantages of Industry 4.0 in textile manufacturing is the implementation of predictive maintenance. Sensors embedded in machinery continuously monitor performance metrics, enabling the prediction of potential equipment failures before they occur. This proactive approach minimizes downtime, extends machinery lifespan, and optimizes production schedules.
- Quality Control and Traceability. Smart production lines utilize artificial intelligence and machine learning algorithms for real-time quality control. Automated inspection systems can detect defects or irregularities in fabrics with a level of precision unmatched by manual inspection. Additionally, the integration of blockchain technology enables traceability throughout the supply chain. It ensures transparency and authenticity in product sourcing and production.
- Customization and Flexibility. Industry 4.0 technologies empower textile manufacturers to respond swiftly to changing consumer demands. Smart factories equipped with flexible manufacturing systems can easily adapt to produce smaller batches of customized products. Computer Numerical Control (CNC) machines and robotic systems, guided by digital design files, enable the rapid and efficient production of diverse textile designs.
- Digital Twin Technology. The concept of a digital twin, a virtual replica of a physical manufacturing system, is gaining traction in textile production. Manufacturers create digital twins of their machinery and processes, allowing for simulation, analysis, and optimization in a virtual environment. This approach aids in identifying bottlenecks, streamlining processes, and experimenting with new production strategies without disrupting actual operations.
- Human-Machine Collaboration. Industry 4.0 is not about replacing human workers but enhancing their capabilities. Collaborative robots, or cobots, work alongside human operators, performing repetitive tasks and heavy lifting. This collaborative approach optimizes efficiency, and improves workplace safety. In addition, it allows human workers to focus on more intricate and value-added aspects of production.
- Data Analytics and Decision-Making. The vast amount of data generated by smart manufacturing processes is harnessed through advanced analytics. Predictive analytics, machine learning algorithms, and artificial intelligence enable manufacturers to gain insights into production patterns, consumer preferences, and operational efficiency. Informed decision-making based on data-driven analysis enhances overall business performance.
- Energy Efficiency and Sustainability. Industry 4.0 contributes to sustainability goals by optimizing energy consumption. Smart manufacturing systems can adjust energy usage based on real-time demand, reducing waste and minimizing the ecological footprint of production. Additionally, the integration of sustainable practices, such as eco-friendly raw materials and waste reduction initiatives, aligns with the broader industry trend towards environmentally responsible manufacturing.
As textile manufacturing embraces the era of Industry 4.0, the industry is witnessing a paradigm shift from traditional production methods to a more intelligent, interconnected, and sustainable future. The synergy between human expertise and technological innovation is not only reshaping how textiles are produced. It also defining a new chapter in the industry’s evolution.
The continued exploration and integration of automation and Industry 4.0 principles are pivotal in shaping a future where textile manufacturing is not only efficient but also environmentally conscious and adaptable to the dynamic demands of the global market. Product lifecycle management like Wave PLM could be a skillful instrument in the era of Industry 4.0.
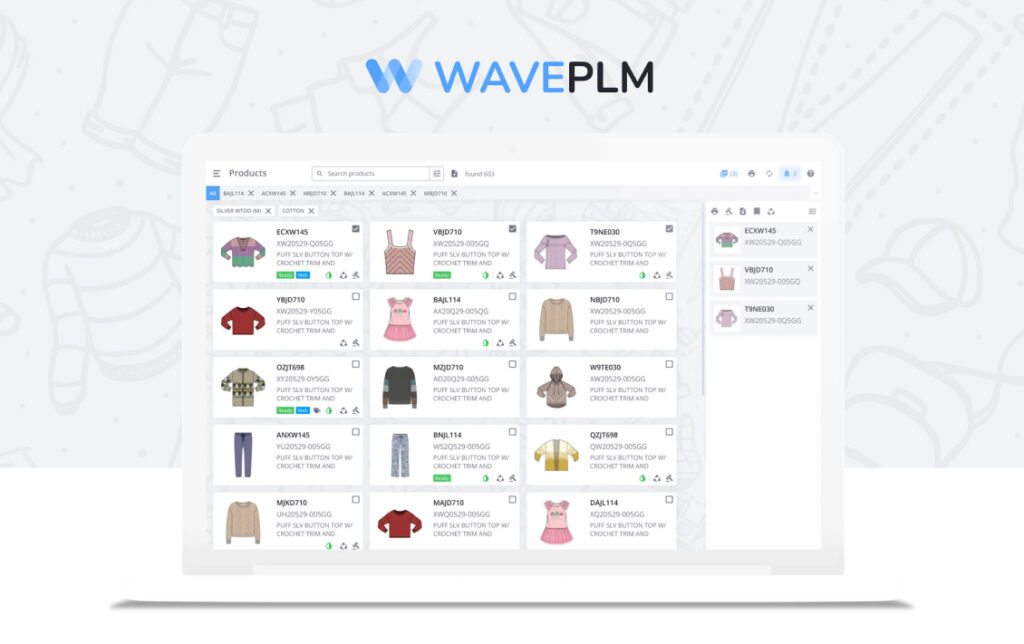
Challenges and Sustainability
While technological advancements have propelled the textile industry into a realm of unprecedented efficiency and innovation, it is not without its challenges. Chief among these challenges is the environmental impact associated with traditional textile manufacturing companies and processes. Issues such as water consumption, chemical usage, and waste generation pose significant concerns, prompting a paradigm shift towards sustainability.
Additionally, water-intensive dyeing processes, once standard practice, are being reevaluated in the wake of water scarcity concerns. Waterless dyeing technologies, such as CO2 dyeing and digital printing, are gaining prominence for their ability to drastically reduce water usage while maintaining vibrant and accurate coloration. These methods not only address environmental concerns but also contribute to cost savings for manufacturers.
Chemical usage in textile manufacturing, ranging from dyeing to finishing processes, has been a longstanding concern due to its potential environmental and health impacts. The industry is responding by exploring eco-friendly alternatives to chemical treatments. It includes the use of natural dyes derived from plants and minerals. Furthermore, the adoption of closed-loop systems for chemical management aims to minimize the discharge of harmful substances into water bodies.
Fashion Recycling
Waste management remains a critical challenge for the textile manufacturing industry. The disposal of textile waste, including off-cuts, unused fabric, and end-of-life products, contributes to environmental degradation. Circular economy principles, emphasizing recycling and upcycling, are gaining traction. Initiatives such as the textile mills into recycling plants and the development of fabrics made from recycled materials contribute to the industry’s commitment to reducing its environmental footprint.
Sustainability in the textile trade and manufacturing extends beyond environmental considerations to encompass the social and ethical dimensions of the cotton industry. The textile industry is increasingly embracing fair labor practices, ensuring the well-being of workers throughout the supply chain. Certifications such as Fair Trade and initiatives promoting transparency in sourcing and production are becoming integral to ethical textile manufacturing.
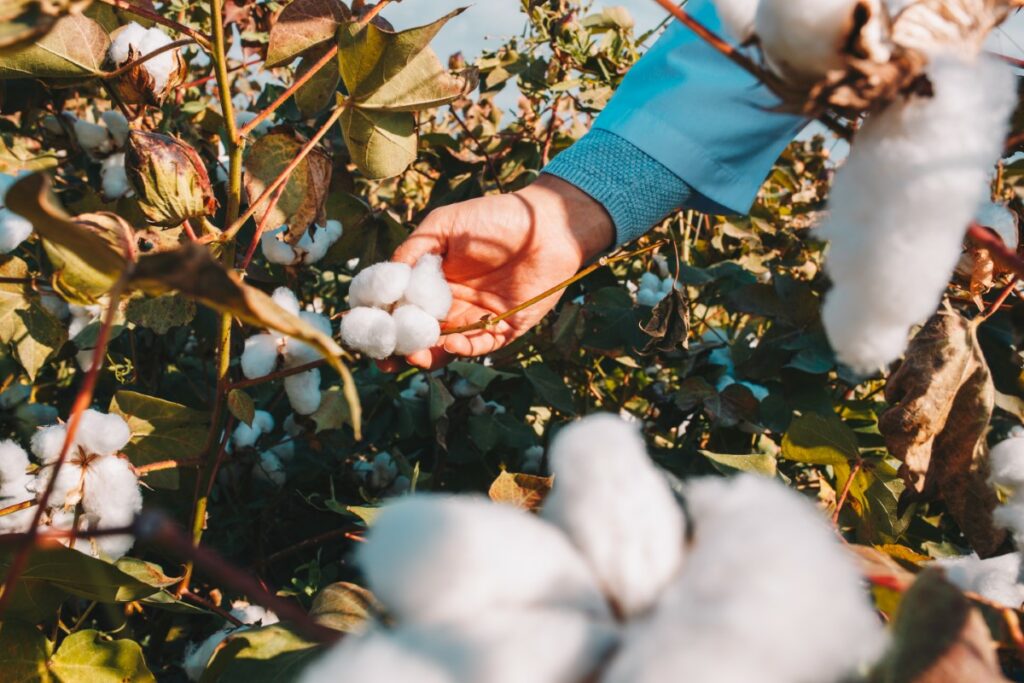
Conclusion
In unravelling the multifaceted dynamics of textile manufacturing, it becomes evident that the industry is a tapestry woven with threads of innovation, tradition, and sustainability. From the meticulous selection of raw materials to textile manufacturing begins the integration of cutting-edge technologies. It is where the textile sector continually shapes and reshapes our relationship with fabrics.
As global demand for sustainable and ethically produced textiles escalates, the textile industry is at a crossroads. It seeks to balance innovation with environmental and social responsibility. The journey from fibers to finished products is a long and complex process of producing textiles. It is a testament to human ingenuity, technological prowess, and a growing awareness of the need for sustainable practices.
Appreciating the intricacies of textile manufacturing offers profound insights into the industry’s past, present, and the myriad possibilities for a sustainable future. As the industry navigates the challenges and embraces opportunities for positive change, it stands poised to redefine not only how we dress but also how we perceive and interact with the fabrics that envelop our lives. The multifaceted dynamics of textile manufacturing are an evolving narrative. As the industry continues to weave its story, it does so with a renewed commitment to a future where threads of innovation and sustainability intertwine seamlessly.
Leave a Reply